Reliability is not even close to being good, despite the fact that the internal structure of forged aluminum alloy is fine, consistent, and flaw free. High-precision forgings of a wide variety of complicated forms may be produced from it with a machining allowance that is only 20% of that of aluminum alloy extending thick plate, resulting in substantial savings in both time and money. Second, it has high heat conductivity. Limitations on temperature variation between starting and stopping the forging process are also present. Heated die forging has the advantage of not causing allotropy transition in aluminum alloys, which improves its performance. The mechanical qualities of the metal may be enhanced by efficient forging mechanical parameter management, which ensures that the metal streamline is distributed uniformly and continuously throughout the forging shape.
Finally, forged aluminum wheels have excellent surface treatment performance and qualities including high density, and the absence of porosity, pinholes, and air holes on the surface. The coating has excellent uniformity, adherence, color harmony, and beauty. Alloy wheels that have been forged are easily machined. As can be seen, forged aluminum wheels offer several desirable properties, including low weight, high specific strength, outstanding toughness, fatigue resistance, corrosion resistance, superior thermal conductivity, and ease of machining. Here we talk about the differences between aluminum alloy forging and aluminum alloy casting.
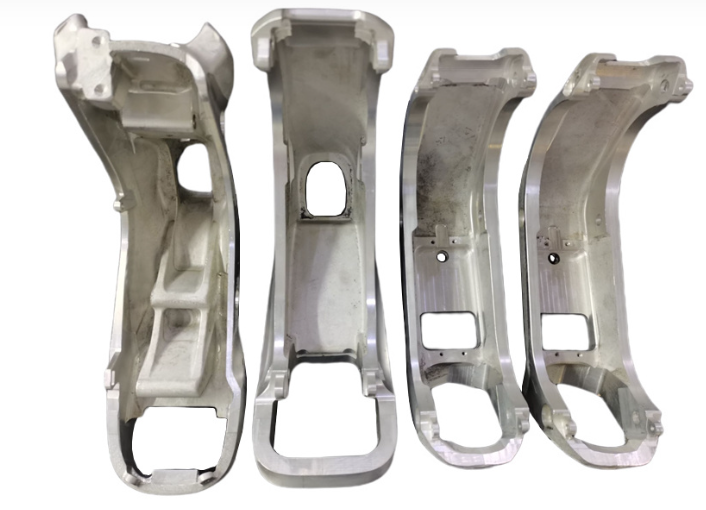
Variations in Forging and Casting of Aluminum Alloys
Aluminum alloy is often forged into various shapes. Die-casting aluminum alloy is a subset of casting aluminum alloy that sees the majority of the practical use.
Both A1 Si Mg Cu alloy and A1 Cu Ni Fe alloy are examples of wrought aluminum alloys. Some examples of frequently used forged aluminum alloys include LD2, LD5, LDl0, etc. They contain many kinds of alloy elements, but less. Their forging qualities are outstanding because of their thermoplasticity, and they also have strong mechanical properties. Die forgings that carry weights, as well as some forgings with complicated forms, are typical applications for this alloy.
Cast aluminum alloys include A1 Si system, A1 Cu system, Al Mg system and Al Zn system. Good casting qualities are just as important as the required mechanical capabilities and corrosion resistance for cast aluminum alloys. A1 Si alloy, commonly known as SiAlMing, is the most desirable cast aluminum alloy due to its excellent combination of casting characteristics and mechanical qualities.
Good casting performance, low density, excellent corrosion resistance, heat resistance, and weldability; used in the production of castings with complex shapes and low strength requirements, such as aircraft and instrument housings; used in the production of castings with complex shapes and medium strength requirements, including motor shells, cylinder blocks, fan blades, engine pistons, and so on.