Difference Between Function of Aluminum Alloy Die Casting & Zinc Alloy Die Casting
Most aluminum and aluminum alloy die castings can be electroplated. Although the technology is more complicated than that of steel, copper and copper alloy electroplating, the technology is now sophisticated and has been put into production and use in large quantities. For example, car hubs are electroplated from aluminum alloy die castings. China has become a large country and the largest exporter of aluminum hub electroplating. Because of the structural problems of some die-casting aluminum alloys, there are sand holes and the silicon content is too high, and electroplating is still difficult.
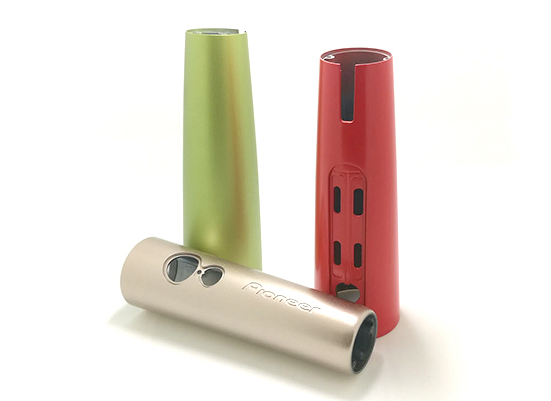
Aluminum Die Casting
Under normal circumstances, aluminum alloy die castings can improve the anti-corrosion function by direct surface oxidation, which is cheap. If used for electroplating, the price will be slightly higher, and the effect may be similar. Due to its good plasticity but low strength, aluminum alloy die castings are suitable for medium structural materials with large load. Aluminum alloy has small density and great hardness.
Aluminum alloy is the most widely used non-ferrous metal structure data in industry. It has been widely used in aviation, aerospace, cars, machinery manufacturing, shipbuilding and chemical industry. With the rapid development of industrial economy, the demand for aluminum alloy welded structural parts is increasing day by day, which deepens the research on the weldability of aluminum alloy. At present, aluminum alloy is the most used alloy.
Electroplating Function of Aluminum Alloy Die Casting & Zinc Alloy Die Casting
As for the electroplating function of aluminum alloy die castings, it is well known that there are many difficulties in electroplating on aluminum because of its vivid chemical properties, poor electrochemical potential, high affinity for oxygen and easy oxidation; The linear expansion coefficient of aluminum is larger than that of ordinary metals. It is also an amphoteric metal, unstable in acid and alkali, and disordered in chemical reaction; The coating has internal stress, so the key to the success of electroplating (or electroless plating) on aluminum is to deal with the problem of adhesion. After the oxide film on the surface of aluminum is removed by acid-base corrosion, it can be rapidly regenerated in air or aqueous solution.
The electroplating function of zinc alloy die castings is much better than that of aluminum alloy die castings. At present, the surface treatment processes of zinc alloy die castings and aluminum alloy die castings are rich and diverse, which are fully utilized by all professions. Each process has its own advantages and disadvantages. Of course, all kinds of imperfections are being continuously improved and innovated by local die-casting mold manufacturers and surface treatment suppliers.
Function of Aluminum Die Casting Vs Zinc Die Casting
Zinc alloy die castings have good casting function, and can cast precision parts with disordered shape and thin wall, and the casting surface is smooth; During melting and die casting, no iron absorption, no corrosion, no die sticking; Good normal temperature mechanical function and wear resistance; Low melting point, melting at 385 ℃, simple die casting.
Both aluminum alloy and zinc alloy have good corrosion resistance. Zinc alloy has higher hardness and tensile strength than aluminum alloy, but there is no definite boundary. Its hardness is very large, and the tensile strength is also relatively good. The main difference between them lies in the composition. The main element of zinc alloy is zinc, which is generally greater than 85%, and the main element of aluminum alloy gold is aluminum, which is generally greater than 87%. The details depend on the variety and trademark of the alloy. A brief understanding is that zinc alloy is an alloy in which other alloy elements are added to zinc, and aluminum alloy is also an alloy composed of other elements based on zinc. Zinc alloy has low melting point, good fluidity (thin-walled parts can be cast), easy fusion welding, brazing and plastic processing, corrosion resistance in dry air and atmosphere, and easy recovery and remelting of residues and wastes; However, the creep strength is low, and natural aging will change the scale. Zinc alloy can be divided into cast zinc alloy and deformed zinc alloy according to the manufacturing process. The output value of cast alloy is much larger than that of deformed alloy.
Composition, Function and Use of Important Zinc Alloys.
– Zinc alloy die castings. According to different casting methods, it can be divided into pressure casting zinc alloy and gravity casting zinc alloy. Pressure casting zinc alloy has been used in the car industry since 1940. It has developed rapidly and its output value has increased sharply. About 25% of the total consumption of zinc is used to produce this alloy. The most commonly used alloy system is Zn Al Cu mg system.
– Aluminum can refine the grain size, improve the strength and impact toughness of zinc, significantly reduce the corrosion of molten zinc to iron containers, avoid the welding or adhesion between castings and die-casting dies, and enable zinc alloys to be produced in hot chamber die-casting machines to improve the yield.
– Copper can improve the strength, hardness and corrosion resistance of zinc alloy, but too much copper will reduce the impact toughness and dimensional stability of the aged alloy. The maximum content of copper in die-casting zinc alloy is 1.25%, and it is best to control it below 1%. If the casting is large or requires high dimensional stability, the alloy with low copper content should be selected.
– Magnesium in die-casting zinc alloy can reduce the corrosion of materials and eliminate the harmful effects of impurities such as lead and tin; The content of magnesium is about 0.01 ~ 0.08%, generally not more than 0.05%. If the content is too much, it will produce thermal brittleness, making casting difficult.
Some impurities significantly affect the function of die cast zinc alloys. Therefore, the content of iron, lead, cadmium, tin and other impurities is strictly limited, with the upper limit of 0.005%, 0.004%, 0.003% and 0.02% respectively. Therefore, high-purity zinc with purity greater than 99.99% should be used as the material for die-casting zinc alloy.
Gravity casting zinc alloy can be cast in sand mold, gypsum mold or hard mold. This zinc alloy not only has the characteristics of general die-casting zinc alloy, but also has high strength, good casting function, cooling speed has no significant impact on mechanical function, residual and waste materials can be recycled, the gate is simple, insensitive to overheating and remelting, small shortening rate, few pores, can be electroplated, and can be finished by conventional methods.