Aluminum alloys forged or cast, but they are fundamentally different materials. Forging and casting are the two main categories of the extrusion process in an extrusion press. Learning how to tell the difference will need some serious research. With the hope of expanding our horizons, we will now educate you on the extrusion press.
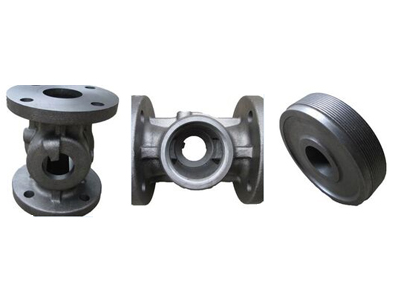
The extruder’s setup is decided by the master cylinder. Forging and casting are also used to categorize the master cylinder. What kind of master cylinder has the most advanced settings? What really differentiates them from one another?
Forging the main cylinder of an extruder is a technique of working with metal whereby the blank is subjected to a high enough pressure to undergo plastic deformation, yielding a finished product with the desired mechanical qualities and dimensions. In the context of plastics processing, forging refers to both forging and stamping.
In the mechanical manufacturing industry, forging is a frequent forming technique. Mechanical qualities of forgings are often better to those of castings of the same material, and forging may remove the as cast looseness and welding holes of metal. Unlike simple rolled plates, profiles, or weldments, forgings are utilized for critical sections subject to high load and extreme operating conditions in equipment.
In the case of the main cylinder of an extruder, the casting process entails injecting a molten alloy into a previously prepared mold, where it will cool and solidify to produce the final product. Sand casting, die casting, investment casting, shell casting, EPC, low pressure casting, gravity casting, etc. are only some of the many types of casting that exist.
In most cases, the mechanical qualities of a material may be improved upon by forging rather than casting. Due to their superior mechanical properties, forgings are often reserved for critical components. Still, forgings have a straightforward form. The forging process requires extensive and expensive dressing for components with intricate geometries. Under the same mechanical stresses, pressure, and temperature, forged and cast components need much less volume and weight. Forged components are essential because of their superior functionality. If you’re shopping for an extruder and notice that it’s more expensive than you’d like, it’s likely because the master cylinder’s arrangement was forged.
Complete extrusion manufacturing lines for aluminum extrusion using an extrusion press typically consist of the following primary pieces of equipment:
1. Machines designed to heat ingots
2. Profile extruder and its ancillary equipment.
3. For immediate quenching after profile extrusion, a water and air quenching mechanism (online quenching) is employed.
4. When extruding profiles, a hot cutting saw is used to cut the head and tail off and split the profile along the center.
5. Once several profiles have been extruded, they must be towed behind a tractor to keep them from bending, twisting, or colliding with one another.
6. It serves as a base for a profile roller table and a material transfer mechanism for a longitudinal conveyor.
7. Conveyor belt that runs transversely through a cooling bed to chill and transport profiles.
8. Profiles may have their tension adjusted and their twists fixed using a straightener.
9. It is a storage platform for transversely transferring profiles to the size equipment and for storing profiles once they have been stretched.
10. Saw, sizing device, inspection table, and other components of the profile sizing sawing apparatus.
11. It’s a load accumulator for use in the automated loading of baskets after profile sawing.
12. Aging furnace for aging heat treatment of profiles.
13. Preheating furnace for heating extrusion die.
14. An aluminum profile extrusion oxidation manufacturing line in this design needs a somewhat greater workshop width, but the length may be reduced. The layout is small and logical, allowing for a tight link between the procedures before and after the extrusion manufacturing line. It allows for the whole manufacturing process to be run automatically and in a continuous manner. A total of just three to five employees are needed to run the aluminum extrusion process.
The difference between forging and casting of extrusion press and the equipment for extruding aluminum profiles
Aluminum profiles are common, such as screens and aluminum windows. It adopts the extrusion process, that is, after the raw materials such as aluminum ingot are melted in the furnace, they are extruded by the extruder to the mold for outflow molding, and it can also extrude various profiles with different sections. Advantages: light weight only 2.8, no rust, fast design change, low mold input, and longitudinal elongation up to more than 10 meters. The appearance of aluminum profiles can be bright or matte. The anodizing process is adopted, and the thickness of the surface treatment oxide film reaches 0.12m/m. The wall thickness of aluminum profile shall be selected according to the optimization of product design. It is not the thicker the better in the market. It shall be designed according to the structural requirements of the section. It can be uneven within 0.5~5mm. The layman thinks that the thicker the stronger, in fact, it is a wrong view.
The surface quality of aluminum profiles also has defects that are difficult to overcome: warping, deformation, black lines, convex concave and white lines. Those with high designer level and reasonable mold design and production process can avoid the above defects. The defects shall be inspected according to the national inspection method, that is, the sight distance is 40~50CM to judge the defects.
Aluminum profiles are widely used in furniture: screen frames, various suspension beams, table legs, decorative strips, handles, wiring ducts and covers, chair tubes, etc., which can be designed and used in a variety of ways!
Although aluminum profiles have many advantages, there are also some disadvantages:
The aluminum without oxidation treatment is easy to “rust”, which leads to performance degradation. Its longitudinal strength is not as good as that of iron products. The wear resistance of the surface oxide layer is easier to scratch than that of the electroplated coating. The cost is higher, which is about 3 to 4 times higher than that of iron products.
Compared with the processing method of profile, the equipment used for die casting alloy is different. Its raw materials are aluminum ingots (about 92% purity) and alloy materials, which are melted in the furnace and then molded in the die casting machine. The shape of die cast aluminum products can be designed like toys, with different shapes, which is convenient for connection in various directions. In addition, it has high hardness and strength, and can be mixed with zinc to form zinc aluminum alloy.
Die casting aluminum forming process includes:
1. Die-casting
2. Rough polishing to remove the die residue
3. Fine polishing
On the other hand, die-casting aluminum production process can only be manufactured with molds. The mold cost is very expensive, which is higher than other molds such as injection molds. At the same time, the mold maintenance is very difficult, and it is difficult to reduce the material when the design is wrong.
Disadvantages of die cast aluminum:
The production and processing quantity should be more each time, so that the cost is low. The cost of products with complex polishing and slow production cycle is about 3~4 times higher than that of injection molded parts. The screw hole shall be larger (4.5mm in diameter) to stabilize the connection force
Scope of application: table foot, console connector, decorative head, aluminum profile seal, table-top and coffee table top, etc., with a wide range.
What is the difference between casting and forging of aluminum alloy materials
No, forged aluminum alloy is mainly used for forging. The die-casting aluminum alloy belongs to the casting aluminum alloy, but it mainly uses the die-casting aluminum alloy.
Wrought aluminum alloys include A1 Si Mg Cu alloy and A1 Cu Ni Fe alloy. The common forged aluminum alloys include LD2, LD5, LDl0, etc. They contain many kinds of alloy elements, but less. Their thermoplastic properties are excellent, so their forging properties are very good, and their mechanical properties are also good. This kind of alloy is mainly used for die forgings bearing loads and some forgings with complex shapes.
Cast aluminum alloys include A1 Si system, A1 Cu system, Al Mg system and Al Zn system. In addition to the necessary mechanical properties and corrosion resistance, cast aluminum alloys should also have good casting properties. Among cast aluminum alloys, A1 Si alloy, also known as SiAlMing, has the best combination of casting properties and mechanical properties.
Cast aluminum alloy has good casting performance, low density, excellent corrosion resistance, heat resistance and weldability; It is used to manufacture castings with complex shapes but low strength requirements, such as aircraft and instrument housings; Manufacturing of low and medium strength castings with complex shapes, such as motor shells, cylinder blocks, fan blades, engine pistons, etc.