Cracks in die casting are a type of defect that can be caused by a variety of factors. Here let’s learn about the causes and prevention methods.
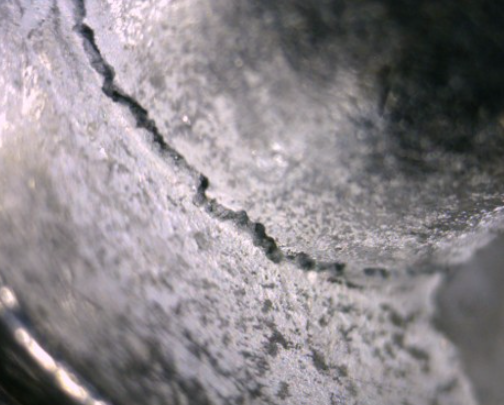
What Are Die Casting Cracks?
Die casting cracks are defects that can occur during the casting process in which cracks or fractures form in the surface or interior of the part. These cracks can cause problems with the strength, durability, and overall quality of the finished product. There are several different types of cracks that can occur in die casting:
1. Hot Cracks: Occurs when the casting is still hot and under pressure which causes small hairline cracks which are visible in the casting after it has been cooled.
2. Cold Cracks: Develops after the metal casting has cooled and the stress builds up due to contraction that results from cooling down.
3. Thermal Fatigue Cracks: This is caused due to metal expansion and contraction due to extreme temperature changes which create elongated cracks in the casting.
4. Residual crack: This type of crack happens when the metal has an uneven cooling rate due to which outer layers solidify first leaving the center of the casting molten. Later on, when the inner layer starts to solidify, it exerts resistance on the already solidified outer layer which causes residual stresses leading to cracks.
5. Thermal Shock Cracks: These cracks occur due to rapid heating or rapid cooling of the casting which causes the material to expand and contract at different rates, leading to cracking.
Does die cast aluminum crack?
Yes, aluminum die casting can crack under certain conditions. Aluminum alloys used in die casting generally have good strength, durability, and high resistance to corrosion. However, they can be susceptible to cracking due to a variety of factors:
1. High-stress levels: Aluminum die cast parts can crack when exposed to high levels of stress. This typically occurs when the part is subjected to a sudden shock or impact force that exceeds its strength, causing it to fracture.
2. Thermal stresses: Thermal stresses can also cause cracks in aluminum die cast parts. These stresses can result from exposure to high or low temperatures, rapid changes in temperature, or uneven cooling rates during the casting process.
3. Fatigue: Repeated or cyclic loading can cause fatigue cracks in aluminum die cast parts. This can occur when a part is subjected to stress over a long period, leading to microscopic cracks that eventually grow and cause the part to fail.
4. Design issues and defects: Poor part design or manufacturing defects can also cause cracking in aluminum die cast parts. For example, excessive wall thickness variations, sharp corners, and inadequate radius can lead to stress concentration and crack formation.
5. Material impurities: The presence of impurities in the aluminum alloy used for casting can reduce its overall strength and increase the risk of cracking. Impurities such as inclusions, porosity, and voids can act as sites of stress concentration, making the part more susceptible to fractures and cracks.
What Causes Cracks in Die Casting?
1. Improper design of the part or mold: Poor part and mold design can lead to excessive stress on the finished product, causing cracks to form. For example, sharp corners, thin walls, or abrupt changes in thickness can lead to stress concentrations that promote crack formation.
2. High casting temperature: If the casting temperature is too high, it can cause thermal stresses, which can lead to cracking. Additionally, high temperatures can cause the release of gas or oxides, which can further weaken the metal and increase the risk of cracking.
3. Inadequate cooling rate: Suboptimal cooling rates can also cause thermal stresses and cracking. The cooling rate must be appropriate for the specific alloy and application to allow for uniform solidification and minimize residual stresses.
4. Injection speed and pressure: Injecting the metal too quickly into the mold or using excessive pressure can cause premature solidification, resulting in incomplete fill of the mold, porosity, and other defects that can promote crack formation.
5. Material selection: Choosing the wrong alloy or impurities in the material can also increase the risk of cracking. For example, high levels of iron or copper can make the alloy more brittle and prone to cracking.
How Do You Prevent Cracks in Casting?
Preventing cracks in casting involves a combination of factors that address material selection, design, and the casting process.
1. Material selection: Choosing the right material for the casting is an essential consideration. The material should be suitable for the application, with the correct mechanical and physical properties to withstand the operational conditions. The material should also be free from impurities that can weaken the casting and increase the risk of cracking, such as inclusions, porosity, and voids.
2. Proper design considerations: The design of the casting should be optimized to minimize stress concentrations that can lead to cracking. This includes avoiding sharp corners and creating transition radii, as well as ensuring uniform wall thickness, smooth surface finishes and appropriate fillet radii.
3. Control of the casting temperature and rate of cooling: Controlling the temperature and cooling rate during the casting process is crucial to prevent cracking. The cooling rate should be optimized to allow for uniform solidification and avoid abrupt thermal gradients that can induce high stresses.
4. Optimization of gating and riser design: Proper gating and riser design can help prevent casting defects and reduce the likelihood of cracking. An optimized gating design ensures that the molten metal flows uniformly into the mold cavity and that any excess material can be vented effectively.
5. Inspection and quality control: Regular inspection and quality control practices should be followed to detect any early signs of cracking or other defects in the casting. This includes visual inspection, non-destructive testing and other methods to ensure the quality of the finished product.