Burr is a term that describes the byproducts of any kind of processing, including but not limited to casting, forging, sintering, welding, air making, blanking, cutting, grinding, electroplating, painting, and insulating coating. Inconsistent with the intended form, burrs and flash are formed on the part’s surface or border during machining. There will be negative effects on the functionality and aesthetics of the machined component. Over the last several years, as the precision of mechanical components has increased, the issue of deburring has risen to the forefront throughout the machining and assembly processes. After that, you’ll learn about four different approaches to deburring cast iron mechanical components.
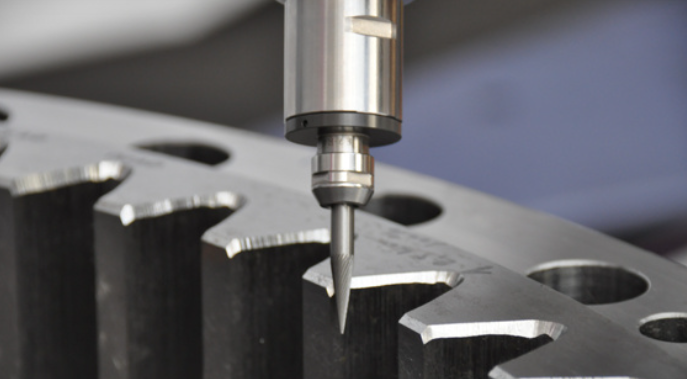
Deburring Method of Cast Iron Machine Parts
Removing burrs using an electric current
The anode will be dissolved with electrical and chemical energy, and the burrs will be removed. The anode is the terminal connected to the positive pole of the DC power source and the component. The cathode, or negative pole, of the DC power source is where the forming tool is attached. In order for the electrolyte to flow freely, a specific distance must be maintained between the two poles. The anode and cathode protrude from the surface of the part because an electrochemical reaction takes place on the anode’s surface when direct current (DC) is applied, causing the dissolved metal and electrolyte on the part’s surface to form a viscous liquid and concentrate in the low recesses of the part’s surface, providing high resistance and low corrosion. The temperature gradient makes it challenging for the liquid film to form. The goal of deburring is to dissolve the burr nearest to the cathode at the quickest rate possible so that the edge progressively becomes a fillet. This occurs after the power line is activated.
In order to remove the burrs, an electrolytic deburring machine might be utilized. Rectifiers are useful for turning AC power into DC power for manufacturing low-volume, low-complexity devices. Special clamps (tool cathode) of conductive materials such as brass or red copper, shaped like the components, are required, and the unprocessed pieces must be coated with epoxy resin for isolation protection. NaCl, NaNO2, and NaNO3 are all examples of common electrolytes.
This technique may be used on both nonferrous and ferrous metal components, and it works particularly well for those with intricate geometries or burrs on internal holes, cross holes, or interior surfaces that are difficult to remove mechanically or by hand. Molybdenum, nickel, titanium, and quenched components are just some of the materials that it can remove burrs from.
Chemical deburring
Metal ions on the surface of the cleaned metal parts will be transported to the chemical solution (50 °C) when the parts are immersed in the solution. In order to prevent corrosion, these ions congregate on the workpiece’s surface, where they react to produce a mucus coating with high resistance and poor conductivity; at the same time, the burrs protrude from the surface and are subsequently eliminated by chemical action. It is sufficient to use a single slot for processing data. Adjust your chemical concoctions for the kind of deburring material you’re working with. Dihydroxyaniline hydrochloride, water, hydrochloric acid, phosphoric acid, sulfuric acid, etc. may all be used as primary components of the base in the right amounts. Tiny metal components may benefit from chemical deburring, which is effective on burrs thinner than 0.07 mm.
Deburring at high temperatures
Seal the chamber tightly with the items to be deburred inside, and then release the hydrogen-oxygen combination at a predetermined pressure. The immediate temperature may reach above 3300 °C once the spark plug causes the mixture to erupt, releasing a great deal of heat. Since there is such little time between when the explosive charge is released and when the bomb detonates, the burr of the component is burnt off while the rest of the part remains unchanged. All internal holes, cross holes, grooves, deep holes, etc., of components may have their burrs burnt off by high-pressure gas entering them during the explosion. A deburring equipment capable of withstanding high temperatures is essential.
This deburring technique may be used on metal, plastic, and rubber components of any structural form, and is particularly useful for those components that are intricate in design and challenging to deburr by hand. To provide the best possible results from the procedure, the correct hydrogen oxygen mixing ratio (the molar mass ratio of hydrogen and oxygen in the seal chamber) must be chosen. The combined gas does not affect steel, alloy steel, or copper. Aluminum alloy is just above the 2:1 mark on the hydrogen oxygen mixing ratio scale. Then, choose the level of inflation (the pressure of mixed gas in the seal chamber). In general, steel and alloy steel have a high inflation pressure, followed by brass and then aluminum alloy. After cleaning and drying, parts are ready to be deburred; after that process is complete, they will go through a neutralization treatment in a phosphoric acid mixed solution to get rid of the oxide deposit.
Rolling and Deburring
Fill a cylindrical container with a mix of work pieces and abrasive materials. Burrs are removed from components by grinding them against one another and against the abrasives while the cylinder rotates. Tumbling and deburring may be done using specialized centrifugal tumbling machines and deburring equipment. Quartz sand, wood chips, aluminum oxide, ceramics, dolomite, silicon carbide, metal rings, and so on may all be used as abrasives. The material, form, and dimensions of the component, as well as the position and size of the burr, should all go into your final decision.
Large burrs may be difficult to eliminate with this approach, but the component deformation is low, the equipment is straightforward, the process is straightforward, the abrasive source is plentiful, and the economics are favorable.