The rapid development of the electronic and electrical fields today not only puts forward higher requirements for the performance and functionality of electronic devices, but also poses challenges to the quality and performance of connectors. The connector housing is a key component of the connector, playing an important role in protecting internal electronic components, ensuring reliable connections, and providing electrical signal transmission and power distribution. In the manufacturing of connector shells, the die casting process for connector shells has become a highly favored manufacturing method.
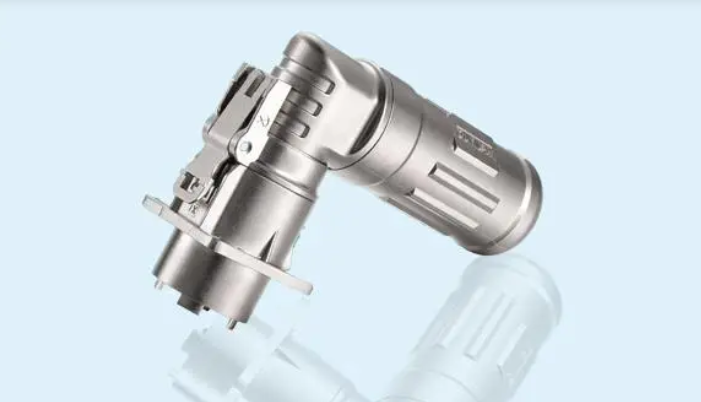
Overview Of Die Casting Process For Connector Housing
The connector shell die-casting process is a highly precise and efficient manufacturing method based on metal alloy materials, which are heated to a liquid state and then injected into the mold under high pressure to form the precise shape of the shell. This process requires the following key steps:
1. Mold design
The successful die casting process for connector shells begins with precisely designed molds. The mold must take into account the shape, size, wall thickness of the outer shell, as well as the internal structure and characteristics of the connector. A carefully designed mold is the key to ensuring the success of the manufacturing process.
2. Material selection
The connector housing needs to have good conductivity, thermal conductivity, and mechanical strength. Therefore, the commonly chosen metal alloys include aluminum, zinc, and magnesium. Different application fields and requirements may require different material choices.
3. Die casting process
During the die casting process, the selected metal alloy is heated to a liquid state and then injected into the mold under high pressure. High pressure ensures that the metal is fully filled in every detail of the mold, thereby achieving precise replication of the shell. This is a key step in manufacturing high-precision and high-quality connector shells.
4. Cooling and Curing
Once the metal is fully filled in the mold, the die-casting part will quickly cool and solidify in the mold. This ensures the precise size and shape of the casing. The control of cooling and curing processes can also affect the final performance of the shell.
5. Mold removal and post-processing
After completing the die casting, the shell needs to be removed from the mold and subjected to deburring, polishing, and other post-treatment processes to ensure that the appearance and performance meet the requirements. These steps help improve the quality and usability of the casing.
Characteristics Of Connector Housing Die Casting
The die-casting manufacturing of connector shells not only has the characteristics of high efficiency and quality, but also emphasizes sustainability and environmental protection. This article will introduce the advantages of connector casing die-casting in sustainable development and environmental protection.
Firstly, the material utilization rate during the die casting process of the connector housing is high. Through precise mold design and optimized die-casting process, we minimize material waste to the greatest extent possible. Compared with traditional processing methods, connector shell die-casting can effectively reduce waste generation, improve material utilization, and reduce resource consumption.
Secondly, the energy consumption during the die-casting process of the connector housing is relatively low. The die-casting machine adopts advanced heating and cooling technology, which can quickly and efficiently heat alloy materials and inject them into the mold to form a connector shell. This efficient energy utilization reduces energy consumption and reduces its impact on the environment.
In addition, the recycling and utilization of die-casting materials for connector shells is also an important aspect of sustainability. The alloy materials used in the die casting of connector shells, such as zinc alloy, aluminum alloy, and magnesium alloy, can all be recycled and reused. By recycling old connector shells and conducting regeneration treatment, we can reduce the demand for raw materials, reduce resource consumption, and achieve the concept of circular economy.
Applications Of Connector Housing Die Casting
Connector casing die-casting is widely used in various fields, including electronics, electrical, communication, and automotive. Here are some important applications of these shells in different industries:
Electronic and electrical fields
The connector housing in electronic devices is used to protect internal circuit boards and components from physical damage and environmental influences.
The electrical connector housing is used for power distribution and control systems to ensure the reliability and safety of current transmission.
Communication field
The connector housing in communication equipment is used to maintain the quality of signal transmission and ensure the stability of data transmission.
In wireless communication equipment, the connector housing must have high anti-interference and waterproof performance.
Automotive industry
The connector housing in the automotive field is used for the connection and protection of electronic control units (ECUs), sensors, and electrical systems.
The quality and reliability of the connector housing are crucial for the performance and safety of automobiles.
The Future Trend of Connector Housing Die Casting
Connector shell die-casting is one of the key processes in the manufacturing industry, and with the continuous progress of technology and changes in market demand, it is also constantly evolving. The following are the future trends of connector casing die-casting:
Material innovation: In the future, connector shells may use more advanced materials to improve performance and adapt to a wider range of applications. For example, lightweight materials, high thermal conductivity materials, and materials with special functionalities may have more applications to meet the needs of different industries.
Enhanced design tools: The development of computer-aided design (CAD) and computer-aided engineering (CAE) tools will enable designers to more accurately predict and optimize the performance of connector shells. This will help reduce design and production cycles.
Digital Manufacturing and Automation: The concept of Industry 4.0 will be more widely applied in connector housing manufacturing. Digital manufacturing and automated production lines will improve production efficiency, reduce costs, and provide higher quality control.
Sustainability and environmental protection: With increasing attention to environmental protection, the manufacturing of connector shells in the future may place greater emphasis on sustainability. This includes using recyclable materials, reducing waste and energy consumption, and adopting more environmentally friendly production processes.
Intelligent connector housing: With the development of the Internet of Things (IoT), connector housing may integrate more intelligent functions such as sensors, communication modules, and data processing capabilities to meet the needs of intelligent devices.
3D printing technology: 3D printing technology is gradually being applied in the field of metal manufacturing, and may play a greater role in the production of connector shells in the future. This will allow for more flexible design and faster prototyping.
Personalized manufacturing: In the future, more personalized and customized connector shells may be seen to meet the needs of specific applications. This will reduce inventory and waste, and improve efficiency.
Changes in global supply chain: Changes in global supply chain and adjustments in trade policies may affect the manufacturing and supply of connector shells. Manufacturers may consider more localized and diversified supply chain strategies.