Common Problems of Aluminum Alloy Die Casting with Solutions | Diecasting-mould
Due to immature technology, unqualified conditions, and some other reasons, there will always be some problems in aluminum die casting, which will affect the casting process and product quality. In this article, we’ll focus on common problems of aluminum alloy die casting and how to solve or improve them.
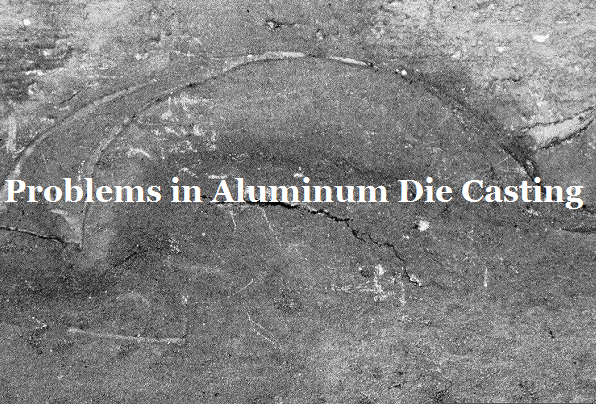
Common Problems of Aluminum Alloy Die Casting - Aluminum Die Casting Tips
The development of die casting services allows the ability to die casting company in new commercial and technical applications. Also, some defects in casting will bring worries.
1. Splashing of molten metal
Reasons:
– There is a gap between the moving mold and the fixed mold.
– The mould locking force is too small.
– The span of the support plate is too large, which leads to the deformation of the sleeve plate.
Solutions:
According to these reasons, what we can do is install new mold, increase the locking force, and add a support plate on the moving die.
2. Cold shut
Reasons:
Cold shut refers to the gap caused by low-temperature metal flow butting with each other but not fused is caused by the following reasons: the alloy composition is not pure or contains impurities, and the fluidity of liquid metal is not strong; poor exhaust and low filling speed; the mold temperature is low and the pouring temperature of molten metal is low.
Solutions:
Change the alloy composition, remove impurities; improve exhaust conditions and increase filling speed; control mold temperature, and pouring temperature.
3. Die failure
Reasons:
Die failure or mould invalidation is caused by material, processing, and other factors, it is presented as hot cracks, wear, sharp corner and corner cracking, erosion, slide block stuck, and other forms in the die casting mold.
Solutions:
To reduce mold invalidation, you should preheat the mold before production to prevent cracking, and set a certain cooling system to prevent periodic thermal expansion and contraction.
4. Undercasting
Reasons:
– Low fluidity and high air content of liquid aluminum.
– Poor casting system, the ingate section is too small.
– Poor exhaust conditions, the exhaust is not smooth, too much coating, mold temperature is too high, resulting in high pressure in the mold cavity, so that the air is not easy to discharge.
Solutions:
– Improve the fluidity of liquid aluminum, especially refining and slag scraping. The pouring temperature and mold temperature should be increased properly. Increase casting speed. Improve the casting structure, adjust the thickness allowance, set up an auxiliary rib channel, etc.
– Increase the cross-sectional area of the gate.
– Improve exhaust conditions, add a liquid flow channel and an exhaust line, and set an exhaust plug is at the deep concave cavity. Make the coating thin and uniform, and then close the mold after drying.
5. Crack
When the blank is damaged or broken, it forms a long and thin crack, which is irregular and linear, comes in penetrating or non-penetrating. The difference between cold crack and hot crack: the metal in the cold crack is not oxidized, and the hot crack is oxidized.
Reasons:
– The casting structure is not reasonable, the shrinkage is hindered, and the casting fillet is too small.
– The ejection device deflects and the force is uneven.
– The mold temperature is too low or too high, and it will crack due to serious strain.
– The harmful elements in the alloy exceed the standard and the elongation decreases.
Solutions:
– Improve the casting structure, reduce the wall thickness difference, increase the fillet and arc, and set process parameters to make the section change smoothly.
– Modify the mold.
– Adjust the mold temperature to the working temperature, remove the inclination and unevenness, and avoid cracking.
– Control the composition of aluminum coating, avoid harmful elements.
6. Bubble & Blister
Under the surface of the casting, the bubbles formed by the accumulated gas bulging.
Reasons:
– Too high mold temperature.
– Too fast filling speed, and the liquid metal flows into the gas.
– The coating has a large amount of gas, which is not volatilized before casting, and the gas is wrapped in the surface of the casting.
– Poor exhaust.
– The mold was opened too early.
– The temperature of liquid aluminum is high.
Solutions:
– Cool the mold to working temperature.
– Reduce the filling speed of the airbag.
– Select the coating with small gas evolution, thin and uniform amount, and close the mold after volatilization.
– Clean and add an exhaust tank.
– Modify the opening time.
– Revise the smelting process.