Sheet metal stamping is a crucial metal plastic forming technology used in aerospace, automotive, electrical machinery, food packaging, daily hardware, construction, packaging, and other industries. Stamping parts’ geometric correctness, mechanical characteristics, and surface quality are affected by forming faults during production. This article will examine the reasons for cracking and wrinkling in stamping and present broad solutions.
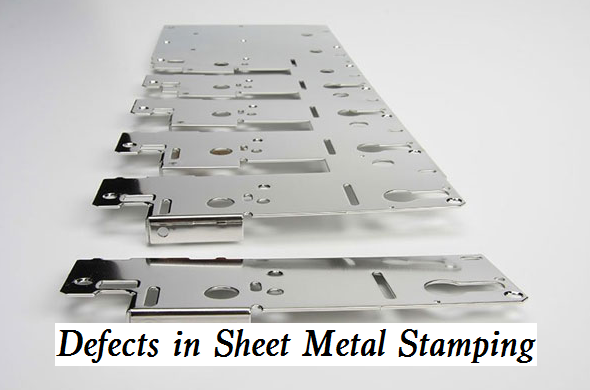
Common Defects Found in Sheet Metal Stamping Process
1. Cracking
Stretching thins sheets. Engineering practice allows a 4%–20% sheet thickness reduction. Too much thinning will weaken the item and perhaps cause sheet breaking and scrap. Thus, cracking is a major fault that degrades stamping parts. As the material tensile test deepens, its bearing area decreases, and its hardening effect increases. When the hardening effect exceeds a particular limit value, the material will first shrink at the weakest bearing capacity and then be ripped off. Similar to the tensile test, sheet metal deforms. Sheet metal breaks at a certain strain.
Microfracture and macrofracture are classified by fracture degree. Sheet metal has microscopic flaws called microfracture. Some materials failed despite the small crack depth. Plate microfracture is apparent. Good-content metal processing WeChat merits attention. Microfracture can be generated by simple expansion or bending, but macrofracture is usually caused by a severe expansion in the thin plate’s plane. Excessive local tensile strain causes microfracture and macrofracture. In the deep drawing process, the punch fillet, the center of the side wall, and the draw bead area fracture cause flow obstruction.
How to prevent cracking defects?
To prevent fractures, modify the distribution of normal contact force and tangential friction force to lower the local tensile strain value. Engineering includes:
1) Choose a suitable blank size and form
Blank size and shape affect sheet metal forming quality. The square blank first stretch the square cylinder. To fix a crack, chamfer the blank’s four corners.
2) Add auxiliary processes (alter the product’s arc or slope, and add plastic or process cuts) If the part’s functional requirements are met, suitably raising the die fillet or reducing the slope will minimize the material’s flow resistance in the forming process, preventing cracking. Punch the appropriate region of the plate to supplement the area prone to fracture with materials from the neighboring area to improve deformation and prevent fracture.
3) Change the draw bead or blank holder force.
Draw beads reduce flange wrinkling but increase material flow resistance into the die. Thus, inappropriate draw bead characteristics may increase flow resistance and sheet cracking.
4) Improve lubrication
Lubricant is crucial to stamping quality. Poor lubrication or lubricant selection can cause sheet breaking.
2. Wrinkling
Stamping defects like wrinkles degrade product surface quality. For example, domestic vehicle aesthetic panel forming quality is poor, and wrinkling is a major reason. Worse, the mold may iron the workpiece and scratch the mold, causing production losses. The instability of the sheet’s thickness direction due to excessive local compressive stress causes wrinkling, not cracking. Compression instability causes this. Wrinkling is perpendicular to compressive tension but not caused by it.
Sheet metal stamping generates material accumulation and unstable wrinkling. Buckling wrinkling is generated by the instability of the compression flange with weak binding force in the sheet metal thickness direction and instability in the uneven tensile portion. Material accumulation wrinkling is caused by too much material entering the die cavity. Wrinkling impairs precision and aesthetics but does not degrade parts like pulling cracks. Wrinkling in the intermediate process may disrupt the next procedure.
How to prevent wrinkling defects?
When the local compressive stress of the material is too high, it is possible to generate wrinkling, especially when the material is under tension and compression stress states. To eliminate wrinkling, precisely forecast the material’s flow and enhance the normal contact force at the wrinkling site. Engineering includes:
1) Increase blank-holder force
The blank holder force can reduce flange edge wrinkling and improve material flow resistance entering the die.
2) Add drawing ribs or height.
Drawbars are round, square, and drawbars. Feed resistance rises. Drawbar use depends on workpiece drawing depth, material qualities, product shape, and more. Reasonably establishing the draw bead, scientifically controlling the feeding resistance, modifying the material’s internal stress condition, and adjusting the material flow direction will improve the wrinkling fault.
3) Shape products and molds to absorb surplus material.