Broadly speaking, automobile mold refers to the mold for manufacturing all parts of the car. For example, injection mold, stamping mold, forging mold, casting mold, glass mold, etc. When people talk about automobiles, the first thing they see is the car body. The automotive mold includes top cover flanging die, cross beam reinforcing plate pressing die, etc.
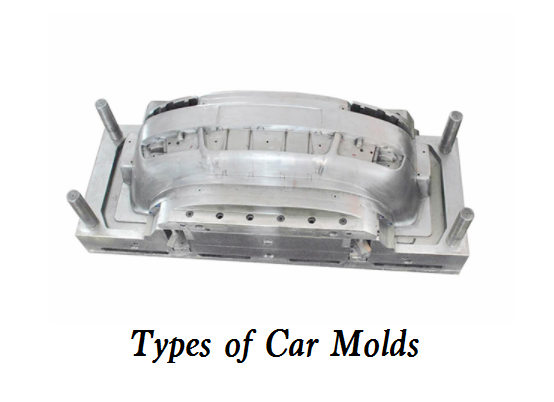
Classification and Types of Car Molds
There are many ways to classify automobile part molds. The different mold types or manufacturing methods of the auto part forming and processing can be divided into the following categories.
Injection mold
Injection mold is also called injection mold. The molding process of this mold is characterized in that the plastic raw materials are placed in the heating barrel of the injection machine. The plastic is heated and melted. Driven by the screw or plunger of the injection machine, it enters the mold cavity through the nozzle and the pouring system of the mold. The plastic is solidified and formed in the mold cavity through heat preservation, pressure holding, and cooling. Because the heating and pressurizing device can play a role in stages, injection molding can not only form plastic parts with complex shapes but also have high production efficiency and good quality. Therefore, injection molding occupies a large proportion of the molding of plastic parts, and the injection mold accounts for more than half of the plastic molding mold. The injection machine is mainly used for the molding of thermoplastics and has gradually been used for the molding of thermosetting plastics in recent years.
Compression mold
Compression die is also called pressing die or glue pressing die. The molding process of this mold is characterized in that the plastic raw materials are directly added into the open mold cavity, and then the mold is closed. After the plastic is in a molten state under the action of heat and pressure, the mold cavity is filled with a certain pressure. At this time, the molecular structure of the plastic produced a chemical cross-linking reaction and gradually hardened and shaped. Compression molds are mostly used for thermosetting plastics, and their molded plastic parts are mostly used for the shell of electrical switches and daily necessities.
Transfer mold
Transfer mold is also called pressure injection mold or extrusion mold. The molding process of this mold is characterized in that the plastic raw materials are added to the preheated feeding chamber, and then the pressure is applied to the plastic raw materials in the feeding chamber by the pressure column. The plastic melts under high temperature and high pressure and enters the cavity through the pouring system of the mold, and then the chemical crosslinking reaction occurs and gradually solidifies and forms. The transfer molding process is mostly used for thermosetting plastics, which can form plastic parts with complex shapes.
Extrusion mold
The extrusion die is also known as the extruder head. The die can continuously produce plastics with the same section shape, such as plastic pipe, bar, sheet, etc. The heating and pressurizing device of the extruder is the same as that of the injection machine. The molten plastic will form continuous molded plastic parts through the machine head, and the production efficiency is particularly high.
In addition to the plastic molds listed above, there are vacuum forming molds, compressed air molds, blow molding molds, low foaming plastic molds, etc.
Molding parts on automobile bodies are generally divided into covering parts, beam frame parts, and general stamping parts. The stamping part that can clearly represent the image characteristics of the automobile is the automobile panel. Therefore, the more specific automobile die can be said to be an automobile panel stamping die. For example, trimming die for front door outer panel, punching die for front door inner panel, etc.