Aluminum ingots are produced using special molds in different sizes and shapes. The casting process of aluminum alloy ingot also exists some technical issues. In this article, we’ll list some common aluminum ingot casting defects, as well as the reasons and causes or tips.
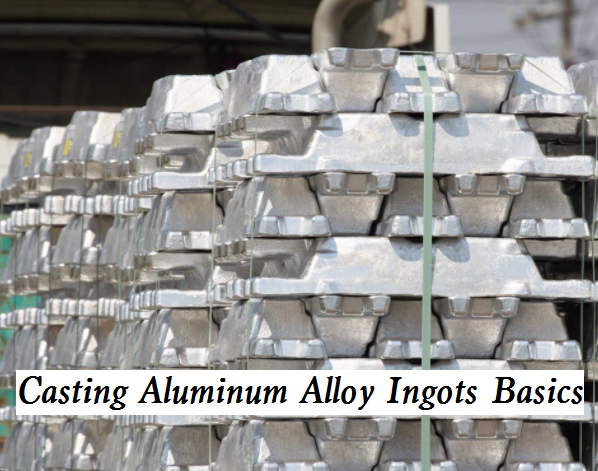
Casting Aluminum Alloy Ingots Basics | Aluminum Ingot Casting Defects
1. The surface of the ingot is uneven, with many honeycomb holes and cracks.
-When the silicon content of the alloy reaches about 12%, the crystallization temperature interval of the alloy becomes narrow, and shrinkage cavity and porosity will occur at the top of the ingot during solidification, which is caused by the nature of the alloy itself and is the characteristic of eutectic silicon aluminum ADC12 alloy, in particular, will produce this phenomenon When the silicon content is below 10.5%, cracking will not occur.
– The shaking (vibration) of the conveyor belt accelerates the solidification of the alloy liquid, resulting in the increase of the depth of shrinkage and porosity, resulting in honeycomb holes, which is caused by external factors and has no impact on the internal quality.
– It is closely related to the proportion of raw and cooked raw materials.
2. The fluidity of molten liquid is poor and it is difficult to die cast.
After any metal melts into liquid, it will produce sediment, leading to metals at different heights, which is closely related to the purity of raw materials After the alloy is prepared, about 10% silicon should be added to the aluminum-silicon alloy The raw metal silicon brings in impurities such as calcium (CA) and iron (FE), and increases impurities such as calcium oxide and ferrous oxide The bottom of the pot is mainly metal compounds and non-metal compounds with impurities, which does not work when the temperature is raised. The spectroscopic test shows that the components are completely out of the sample and can not be used for casting parts. Therefore, we should pay attention to:
– When the aluminum alloy ingot is melted out of the liquid, the bottom material must be isolated and separated, and cannot be mixed into the soup to cast the ingot.
– In the process of die casting, each crucible aluminum soup needs to clean the sediment at the bottom of the pot and the crucible when pouring to a certain residual amount. It is not allowed to continuously add pouring risers, waste castings, and flash aluminum chips in the pouring process so that the sediment at the bottom of the pot gradually accumulates, and finally form a pot of aluminum soup, which is sticky and paste, which not only loses fluidity but also is very difficult to clean the pot This often happens to many domestic users.
3. It is easy to stick the mold and the demoulding is not smooth.
– The quality of the selected release agent is not good, such as water agent graphite release agent, which leads to the casting can not slide out of the mold cavity smoothly
– The impurity content in the alloy exceeds the standard
– Mold demoulding slope is too small so that demoulding is not smooth
– There are too many cracks in the old mold, resulting in mold sticking
– If the iron content in the alloy is too low, which is lower than the standard range required by the die-casting process, it will also cause die sticking
4. There is slag inclusion in the aluminum ingot section, and the molten metal produces continuous golden yellow scum and black suspended particle scum.
In the melting process of aluminum alloy, fluxes such as slag remover, modifier, and magnesium remover are commonly used. The raw materials of these additives are mainly composed of fluoride, nitrate, and chloride. These halogen alkali element compounds will cause golden scum when volatilized; The generation of black suspended particle scum is mainly because the melting point of silicon is as high as 1412 ℃. In the process of aluminum alloy melting, if the silicon is not completely melted into solid solution according to the operating procedures, the primary silicon exists in the aluminum soup and floats on the liquid surface in a black suspension Therefore, the slag removal process must not be careless. It must be operated according to the process procedures, and the flux composed of carbonate, sulfate, and nitrate shall be selected to make the chemical reaction products form dry slag that is easy to be separated from the liquid aluminum.
5. After strict degassing steps, the gas cannot be removed from the molten liquid.
The aluminum alloy degassing process has been improved, including the inert gas degassing and solid flux degassing method. Gas degassing includes chlorine, argon, and nitrogen, as well as three gas degassing methods; Solid flux degassing agents include hexachloroethane, carbon tetrachloride, sodium nitrate, non-toxic degassing agent, etc. As long as the operation is reasonable, the gas (H2) in the molten aluminum can be removed The primary condition of degassing flux is that it cannot contain gas. Here, gas refers to hydrogen (H2) from water (H2O). Therefore, degassing flux itself has extremely strict requirements on gas content, and dehydration treatment shall be carried out during generation Sometimes the gas cannot be removed even after degassing operation, which is often caused by the poor quality of the degassing agent. For example, the moisture content in the degassing agent is too high, the degassing agent is placed for too long, the flooding deterioration is not fresh, and so on.
6. The nozzle is cracked during mold opening.
– The mold design and manufacture are unreasonable, and the length of the ejector rod is inconsistent when opening the mold.
– Unreasonable design of ejection position.
– Raw materials are brittle and not tough enough.
7. The casting is brittle during post-treatment (polishing, finishing, and drilling), and the casting is easy to break.
– Aluminum silicon alloy has high silicon content, brittle material, and easy fracture.
– Embrittlement and cracking can also be caused by too long heat preservation and storage time of aluminum alloy liquid or overheating of alloy liquid.
8. The confluence of castings cannot be fully fused and obvious boundary marks remain.
– This defect can be caused by low alloy liquid temperature or low die temperature and poor fluidity of alloy liquid. The main reason is that the two liquid streams cannot be fused.
– Low filling speed.
– Unreasonable mold design and improper distribution position of the overflow tank.
– Low specific pressure; The structure and size of each casting are different, and the correct casting process should be designed according to the actual object.