Cast iron is a versatile and widely-used material known for its durability and strength. Within the realm of cast iron, there exist several distinct varieties, each with its own unique properties and applications. In this exploration, we delve into three prominent types of cast iron: Grey Cast Iron, Vermicular Graphite Cast Iron, and Ductile Iron. Each of these materials offers a different set of mechanical characteristics, making them suitable for a wide range of industrial and engineering purposes. Let’s navigate through the individual qualities and best-suited applications of these cast iron variants, providing a comprehensive understanding of their significance in the world of materials and manufacturing. Today, we’re going to talk about material characteristics and structural characteristics of cast iron and cast steel.
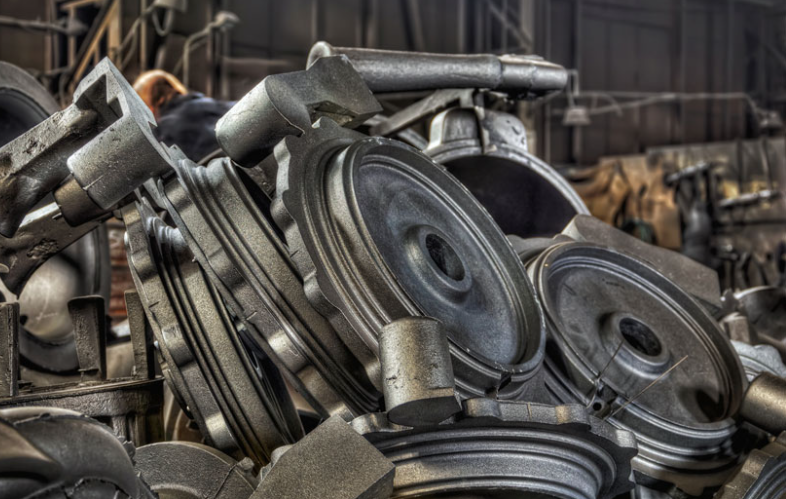
Cast Iron: Understanding Grey, Vermicular, and Ductile Iron
1. Grey Cast Iron
Grey cast iron is a cast iron containing flake graphite, which is the most widely used cast iron, accounting for over 80% of the total production of cast iron. Grey cast iron material has low comprehensive mechanical properties and high compressive strength, which is 3 to 4 times its own tensile strength. The vibration damping capacity is 10 times greater than that of steel, so it is often used to manufacture frames that withstand vibration. The elastic modulus is low, and the change in wall thickness has a significant impact on mechanical properties. Due to its high sensitivity to cooling rate, gray cast iron castings often exhibit white spots and cracks on thinner sections, while on thicker sections, it often leads to looseness.
Therefore, there is a critical value for the cross-sectional thickness of gray iron castings. If this value is exceeded, the mechanical properties such as strength, vibration damping capacity, and elastic modulus will not increase as the wall thickness increases, but will significantly weaken. Due to the low thermal stability of gray cast iron, it cannot be used to manufacture parts that work for extended periods of time in environments exceeding 250 degrees Celsius. Compared to cast steel materials, using gray cast iron can obtain castings with thinner thickness and more complex geometric shapes, and the residual internal stress and warping deformation in the castings are smaller. Due to the relatively uniform performance on each cross-section, gray cast iron is often used for manufacturing castings with high requirements, but the cross-section may not necessarily be thicker.
2. Vermicular Graphite Cast Iron
Vermicular graphite cast iron is a vermicular cast iron, with a graphite morphology between flake and spherical, and a chemical structure similar to gray cast iron. The comprehensive mechanical properties of vermicular graphite cast iron are slightly better than gray cast iron, but slightly inferior to ductile iron. Its impact toughness, elongation, compressive strength, yield strength, etc. are all between the two, and the impact of wall thickness changes on mechanical properties is smaller than that of gray cast iron. Vermicular graphite cast iron is much less sensitive to cooling rate than gray cast iron and has good thermal conductivity, so it is often used to manufacture parts with harsh working environments and large temperature gradients.
Due to its high strength, good compactness, low sensitivity to notches, and excellent process performance, vermicular graphite cast iron materials can be used to manufacture large parts with complex geometric shapes. In order to save scrap steel and reduce the weight of castings, vermicular graphite cast iron can also be used as a substitute for inoculation cast iron. This can also effectively improve the yield and enhance the airtightness of castings, making it particularly suitable for the production of hydraulic components.
3. Ductile Iron
The spherical graphite obtained through spheroidization and inoculation treatment is called nodular cast iron. It is a high-strength cast iron material developed in the middle of the last century, with high comprehensive properties, similar to steel, and has a very wide range of industrial applications. Ductile iron has better strength, plasticity, and elastic modulus than gray cast iron, and its wear resistance is twice that of gray cast iron. The change in wall thickness has little impact on mechanical properties, but its vibration damping capacity is lower than that of gray cast iron.
Although ductile iron has a high sensitivity to cooling rate, due to its high thermal stability and strong resistance to high temperatures, it can be used to manufacture parts that work in environments ranging from 300 to 400 degrees Celsius. Its mechanical properties are less affected by changes in chemical composition, resulting in a higher yield compared to other cast iron materials. Due to the high volume shrinkage rate and low linear shrinkage rate, it is easy to form shrinkage cavities and porosity. Ductile iron castings are usually designed with uniform thickness.
Differences Between Grey Cast Iron, Vermicular Graphite Cast Iron & Ductile Iron
The question of which type of cast iron is “better” depends on the specific application and the properties you require. Each type of cast iron—Grey Cast Iron, Vermicular Graphite Cast Iron, and Ductile Iron—has its own advantages and disadvantages, making them better suited for different purposes. Here’s a brief comparison:
- Grey Cast Iron:
- Advantages: High compressive strength, excellent vibration damping capacity, and often used for parts that need to withstand vibration. Ideal for applications where internal stresses and warping deformation must be minimized.
- Disadvantages: Limited thermal stability (not suitable for high-temperature environments above 250 degrees Celsius), sensitivity to cooling rate can lead to defects in thinner sections.
- Vermicular Graphite Cast Iron:
- Advantages: Better mechanical properties than Grey Cast Iron, less sensitive to cooling rate, good thermal conductivity. Ideal for parts with harsh working conditions and large temperature gradients. Suitable for large and complex geometric shapes.
- Disadvantages: Slightly inferior to Ductile Iron in terms of mechanical properties.
- Ductile Iron:
- Advantages: High strength, excellent ductility, and elastic modulus similar to steel. Offers better wear resistance and can work in high-temperature environments (300-400 degrees Celsius). Less affected by changes in chemical composition.
- Disadvantages: Lower vibration damping capacity compared to Grey Cast Iron.
The “better” choice depends on your specific needs. For example:
- If you need parts with high compressive strength and vibration damping, Grey Cast Iron may be suitable.
- If you require parts with better mechanical properties and resistance to temperature variations, Vermicular Graphite Cast Iron might be preferred.
- If you’re looking for high-strength components with excellent ductility and wear resistance, Ductile Iron is a good option.
Ultimately, the choice of cast iron depends on the mechanical properties, thermal stability, and other specific requirements of your application. It’s essential to consider these factors and consult with materials engineers or experts when making your selection.