Nickel plating is a common surface finishing method for castings like cast aluminum and cast iron, for other castings, you can also go with other metal plating techniques.
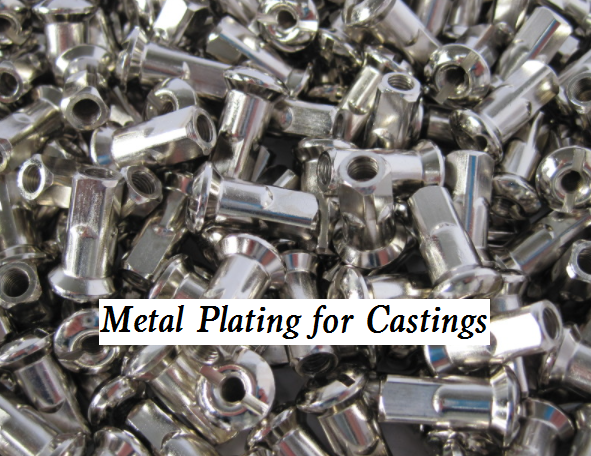
Can You Nickel Plate Cast Aluminum?
Yes, it is possible to nickel plate cast aluminum. Nickel plating is a process that involves electroplating a layer of nickel onto a metal surface to enhance its corrosion resistance, hardness, and wear resistance. However, before nickel plating can be performed, the aluminum surface must be properly prepared to ensure good adhesion of the nickel coating. The aluminum must be cleaned thoroughly to remove any oils, grease, or other contaminants that can interfere with the plating process.
Once the aluminum surface has been cleaned, it must be pre-treated with an appropriate solution to promote the adhesion of the nickel plating. This typically involves the use of an acid or alkaline etching solution to roughen the surface of the aluminum, followed by a nickel strike solution to provide a layer of nickel that will bond tightly to the aluminum. After the surface preparation is complete, the aluminum can be plated with nickel using an electroplating process. The plating process involves immersing the aluminum part in a solution containing nickel ions and then applying an electric current to the solution to deposit the nickel ions onto the aluminum surface.
Can You Nickel Plate Cast Iron?
Yes, it is possible to nickel plate cast iron. Like aluminum, cast iron is a popular material for nickel plating because the resulting coating can improve the surface properties such as wear resistance, corrosion resistance, and hardness.
To nickel plate cast iron, the surface must first be prepared as well. The surface preparation typically involves cleaning and degreasing the cast iron part to remove any dirt, oil, or grease. After cleaning, the part must be roughened to promote adhesion of the nickel plating. This can be done by using an acid etching solution, which can help to create a surface texture that will bond well with the nickel plating.
One important consideration when nickel plating cast iron is the potential for hydrogen embrittlement, a phenomenon that can occur when hydrogen gas is produced during the electroplating process and becomes trapped in the cast iron. To prevent hydrogen embrittlement, it is important to use the appropriate plating conditions and post-treatment steps to minimize the hydrogen content in the cast iron part.
Nickel plating is a versatile surface finishing process that can be applied to lots of other materials, including steel, copper, brass, zinc and stainless steel.
How to Choose the Best Plating Techniques for Castings?
The best plating for castings depends on the specific application and the properties that are desired for the finished product. Some of the most common plating options for castings include:
Zinc Plating: Zinc plating is a cost-effective plating option that provides good corrosion resistance and a bright, decorative finish. It is often used for castings that will be exposed to harsh environments or that require a high degree of corrosion resistance.
Nickel Plating: Nickel plating is a versatile plating option that can provide improved corrosion resistance, wear resistance, and a decorative finish. It is often used for castings that will be subjected to wear and abrasion, as well as those that require a bright, lustrous finish.
Chrome Plating: Chrome plating provides excellent corrosion resistance and a high degree of hardness, making it ideal for castings that will be subjected to wear, abrasion, or high temperatures. It is often used for automotive parts, motorcycle parts, and other applications that require a durable, high-performance coating.
Gold Plating: Gold plating is a decorative plating option that is often used for castings that require a high-end, luxury appearance. It provides a bright, lustrous finish that is highly resistant to tarnishing and corrosion.
Overall, the best plating for castings depends on the specific application and the properties that are desired for the finished product. It is important to consider factors such as corrosion resistance, wear resistance, hardness, and appearance when selecting a plating option for castings.