Bronze casting is a manufacturing process to create intricate parts with the desired shape, what are common casting methods and bronze materials used? Here we’ll go over the benefits, alloys, cost, methods, temperature, and more of bronze casting.
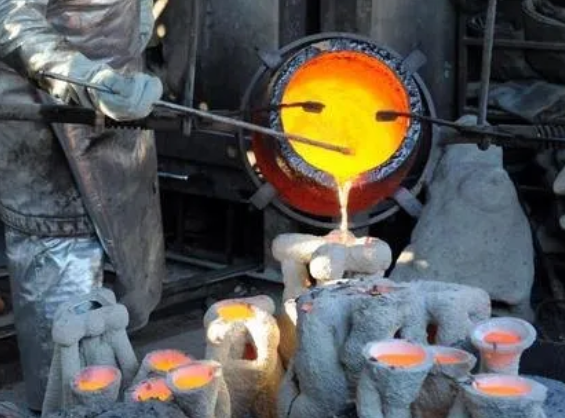
What Is Bronze Casting?
Bronze casting is the process of creating a positive sculpture or object by pouring molten bronze into a hollow mold. Various methods are employed for bronze casting, each with its advantages and disadvantages. The common methods for bronze casting include lost wax casting, sand casting, and ceramic shell casting. Bronze casting can be a cost-effective method for producing small to medium-sized quantities of complex parts or decorative objects.
Why is bronze used for casting?
– Durability: Bronze is a strong and durable metal that can withstand wear and tear, making it suitable for use in objects and structures that need to last a long time.
– Workability: Bronze is a malleable metal, which means it can be easily molded and shaped using various techniques like casting, forging, and bending. This makes it an ideal material for creating intricate and detailed designs.
– Corrosion resistance: Bronze has natural corrosion resistance due to the presence of copper and other alloying elements, making it suitable for use in outdoor applications.
– Aesthetic appeal: Bronze has a unique golden color that can be polished to a high shine. This makes it a popular material for creating decorative objects like sculptures, jewelry, and architectural detailing.
Is it expensive to cast in bronze?
Casting in bronze can be expensive compared to other materials, such as aluminum or certain types of plastics, mainly due to the cost of the raw materials. Bronze is an alloy made primarily of copper and tin, which can be relatively costly, and its price can vary depending on factors like the current market demand, availability and quality of raw materials, and the quantity being purchased. Moreover, the cost of casting in bronze can be influenced by several factors such as the size and complexity of the object, the number of castings needed, and the chosen casting method. In general, small and simple castings are less expensive than larger and more intricate ones, and some casting methods may require more or less labor or post-processing than others, thus affecting the final cost. However, despite the higher upfront cost, casting in bronze can be a good investment due to its long-lasting durability, high-quality finish, and aesthetic appeal.
Bronze alloys for casting
1) Silicon Bronze – commonly used in casting sculptures, statues, and architectural elements. It has excellent corrosion resistance and can be cast into intricate shapes and fine details.
2) Phosphor Bronze – notable for its high strength and wear resistance, making it suitable for creating gears and bearing surfaces.
3) Aluminum Bronze – known for its high strength and corrosion resistance. It is used in casting heavy-duty machine parts, marine hardware, and electrical connectors.
4) Manganese Bronze – has good wear resistance and is often used in casting bushings, bearings, and gears.
At what temperature does bronze melt?
The temperature at which bronze melts depends on the specific composition of the alloy. Bronze is an alloy made from copper and usually contains other metals as well, such as tin, aluminum, or nickel, which can affect its melting point. Here are the approximate melting temperatures of some common bronze alloys.
Silicon Bronze: melts at around 1860°F (1015°C)
Aluminum Bronze: melts at around 1900-1950°F (1038-1066°C)
Phosphor Bronze: melts at around 1650-1880°F (899-1027°C)
Manganese Bronze: melts at around 1740-1915°F (949-1046°C)
Processes and Methods of Bronze Casting
1) Sand Casting – a traditional method in which a mold made of sand is created in the desired shape using a pattern. The mold is then filled with molten bronze and allowed to cool.
2) Lost-wax Casting – another traditional method in which a wax model of the desired object is created. This model is then coated in ceramic, and the wax is melted out, leaving a hollow ceramic mold. The mold is then filled with molten bronze and allowed to cool.
3) Centrifugal Casting – a method in which the molten bronze is poured into a mold that is spinning rapidly on a vertical axis. The centrifugal force ensures that the bronze is evenly distributed throughout the mold, resulting in a dense and high-quality casting.
4) Continuous Casting – a modern method in which molten bronze is poured into a rapidly rotating mold that is cooled with water. This produces thin, continuous strips of bronze that can be cut and shaped into desired forms.
Can you cast bronze at home? It is possible to cast bronze at home using certain equipment and techniques, but it can be a complex and challenging process that requires specialized knowledge and safety precautions. Some of the basic steps involved in casting bronze at home include:
– Creating a mold: The first step involves creating a mold of the desired object using materials such as sand, plaster, or silicone. This process can be time-consuming and require careful planning to ensure the mold is correctly sized and constructed.
– Melting the bronze: Once the mold is prepared, the bronze must be melted in a furnace or kiln to a temperature of around 2000°F, and then carefully poured into the mold.
– Post-processing: After the bronze cools and solidifies, the casting must be removed from the mold and any excess metal or rough surfaces must be polished or removed through various post-processing techniques.