The use of clearance holes can ensure proper fit and ease of assembly when assembling mechanical parts with bolts and screws! To let the fastener pass through freely without engaging the threads, the clearance hole size for different fasteners must be calculated and designed specifically. For example, what is the clearance drill hole diameter for the M10 bolt or #8 screw? Here we explain what a clearance hole is, how to determine and calculate its size, and present standard size charts for both metric and imperial systems.
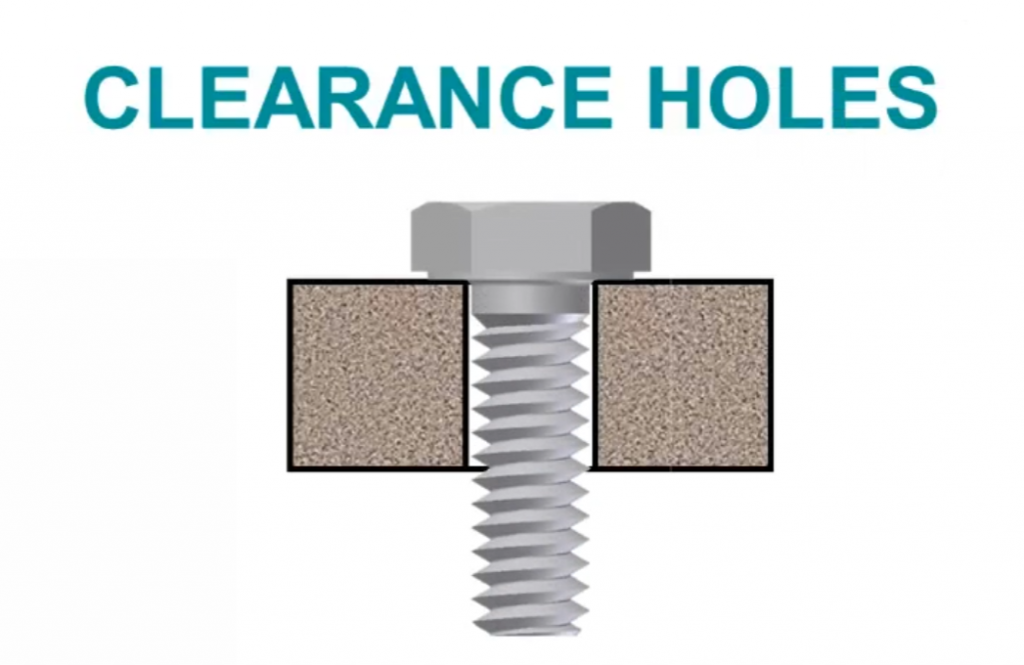
1. What is a Clearance Hole for Screws, Bolts, Studs & Other Fasteners?
A clearance hole is a hole machined into a part or material that is deliberately made larger than the diameter of a bolt or screw to allow the fastener to pass through freely, without the threads engaging with the material. Simply, Such holes are set between two adjacent parts to maintain a certain gap, usually used to ensure that parts can move or adjust freely during assembly or use, avoiding friction, wear, or jamming caused by close fit.
What Purpose of a Clearance Hole?
The core function is to provide assembly adjustment space for screws to avoid interference caused by processing errors or thermal expansion and contraction. For example, the clearance hole of M5 screws is often designed to be 5.3-5.5mm, leaving a gap of 0.3-0.5mm (refer to ISO 273 standard). The function of the clearance hole is mainly reflected in ensuring the flexibility and reliability between parts. By setting appropriate clearance holes, the friction resistance of parts during assembly and use can be effectively reduced, and the overall performance and service life of the product can be improved. At the same time, the clearance hole can also play a role in heat dissipation and weight reduction, which is of great significance in certain specific application scenarios.
What is a Clearance Hole Used For?
When assembly errors need to be compensated, materials that are easy to deform (such as aluminum alloys) need to avoid stress concentration.
So clearance Hole is suitable for scenarios that require frequent disassembly or dynamic loads, such as sheet metal connections, adjustable brackets, etc. The application scenarios of clearance holes are relatively specific, mainly appearing in situations where a certain gap between components needs to be maintained. For example, in electronic products, in order to ensure that the components on the circuit board will not be squeezed or damaged by each other due to thermal expansion and contraction during assembly and use, clearance holes are usually set between components; in mechanical equipment, clearance holes are often used to adjust the clearance of components such as bearings and guide rails to ensure the normal operation and precision requirements of the equipment.
2. How to Determine the Clearance Hole Sizes?
The clearance hole is defined as a hole through an object which is large enough to enable the threads of a screw or bolt to pass through, but not the head of the screw or bolt.
Clearance hole size is determined based on several main parameters:
- Nominal diameter of the fastener: The basic diameter of the screw or bolt you plan to use (for example, 1/4″ or M6).
- Type of fit required: Close fit, normal fit, or loose fit, depending on the application.
- Tolerances for assembly: How much play or accuracy is necessary for proper assembly and function?
- Nominal Screw Size: This is the standard diameter of the screw or bolt for which the clearance hole is being designed.
- Nominal Inch Drill Size: This is the closest standard inch drill bit size used to create the clearance hole for the fastener.
- Nearest Metric Drill Size: This is the closest standard metric drill bit size that can be used to drill the clearance hole.
- Minimum Hole Diameter: This is the smallest allowable diameter for the clearance hole to ensure the fastener passes through freely.
- Maximum Hole Diameter: This is the largest allowable diameter for the clearance hole to prevent excessive looseness of the fastener.
To determine the clearance hole size:
Consult a tap and clearance drill chart for the fastener size and fit type required. For example, for a 1/4″ fastener:
- Close fit: Drill size F (0.257″)
- Loose fit: Drill size H (0.266″)
If greater precision is needed (for example, to ensure assembly under worst-case tolerances), calculate the required clearance hole using the specified fastener size and tolerances.
Always use a center or spot drill to start the hole and minimize wandering, ensuring the hole is accurately positioned and sized.
Design Clearance Hole Size on CAD (SolidWorks):
Clearance holes can be designed in CAD using engineering software or standard size tables. In SolidWorks, for example, the clearance hole function is mainly used to achieve precise clearance control between parts. By setting the parameters of the clearance holes, such as hole diameter, hole depth, tolerance (normal, close, loose fit), etc., holes that meet the clearance requirements can be automatically generated. Clearance holes are used in the design and manufacture of precision-fit parts, such as bearings, gears, transmission shafts, etc.
Application Example:
Taking a bearing seat as an example, it is necessary to design a hole that can have a clearance of 0.01mm with the inner ring of the bearing. Using the clearance hole function, holes that meet the clearance requirements can be automatically generated. By adjusting parameters such as hole diameter, hole depth, and tolerance, precise matching between parts can be ensured.
What is the Clearance Hole Diameter?
The clearance hole diameter is the diameter of the hole that is large enough to permit the threads of a bolt or screw to pass through freely, but not the head. The clearance hole is usually made just slightly larger than the major diameter of the fastener. For example, for a 1/4″ bolt (0.250″ diameter), a clearance hole might be 0.257″ for a close fit or 0.266″ for a free fit, as specified in clearance drill charts.
What is Clearance Hole Tolerance?
Clearance hole tolerance is the allowable variation in the diameter of the clearance hole, ensuring that holes are neither too tight (causing assembly problems) nor too loose (causing excessive movement).
Clearance hole tolerance is typically divided into three categories based on fit:
- Close Fit: Tight tolerance, minimal clearance above the fastener diameter (e.g., 0.257″ hole for a 1/4″ bolt).
- Normal (Standard) Fit: Moderate clearance, general-purpose applications.
- Loose (Free) Fit: Largest tolerance, allows the most play for easy assembly (e.g., 0.266″ hole for a 1/4″ bolt).
For Example:
If we want a close fit, we’re going to use drill size F (0.257″), or if we’re going to use a free fit, we’re going to use a drill size H (0.266″).
Manufacturing tolerances (for example, +0.007″ / –0.002″) are applied to the nominal drill size to account for variability in machining. The fit type chosen (close, normal, or loose) determines the nominal hole size and the amount of clearance.
3. Clearance Hole Size Chart (Hole Diameter, Drill Size, Tolerance) for Screws & Bolts
The charts below display a variety of common screw sizes and their recommended clearance hole diameters, drill sizes, and tolerances for Normal Fit, Close Fit, and Free Fit; each fit is specifically toleranced so that the screw threads can pass through while the head cannot, with Free Fit providing a larger allowance and Close Fit offering a tighter, more precise clearance.
Metric Clearance Hole Chart in MM (with Tap Drill) | ||||||||||
---|---|---|---|---|---|---|---|---|---|---|
Nominal Screw Size | Fit Class – Normal | Fit Class – Close | Fit Class – Loose | Tap Drill | ||||||
Nominal Drill Size | Min. Hole Diameter | Max. Hole Diameter | Nominal Drill Size | Min. Hole Diameter | Max. Hole Diameter | Nominal Drill Size | Min. Hole Diameter | Max. Hole Diameter | Drill Size | |
M1.6 | 1.8 | 1.8 | 1.94 | 1.7 | 1.7 | 1.8 | 2 | 2 | 2.25 | 1.3 |
M2 | 2.4 | 2.4 | 2.54 | 2.2 | 2.2 | 2.3 | 2.6 | 2.6 | 2.85 | 1.6 |
M2.5 | 2.9 | 2.9 | 3.04 | 2.7 | 2.7 | 2.8 | 3.1 | 3.1 | 3.4 | 2.1 |
M3 | 3.4 | 3.4 | 3.58 | 3.2 | 3.2 | 3.32 | 3.6 | 3.6 | 3.9 | 2.5 |
M4 | 4.5 | 4.5 | 4.68 | 4.3 | 4.3 | 4.42 | 4.8 | 4.8 | 5.1 | 3.3 |
M5 | 5.5 | 5.5 | 5.68 | 5.3 | 5.3 | 5.42 | 5.8 | 5.8 | 6.1 | 4.2 |
M6 | 6.6 | 6.6 | 6.82 | 6.4 | 6.4 | 6.55 | 7 | 7 | 7.36 | 5 |
M8 | 9 | 9 | 9.22 | 8.4 | 8.4 | 8.55 | 10 | 10 | 10.36 | 6.8 |
M10 | 11 | 11 | 11.27 | 10.5 | 10.5 | 10.68 | 12 | 12 | 12.43 | 8.5 |
M12 | 13.5 | 13.5 | 13.77 | 13 | 13 | 13.18 | 14.5 | 14.5 | 14.93 | 10.2 |
M14 | 15.5 | 15.5 | 15.77 | 15 | 15 | 15.18 | 16.5 | 16.5 | 16.93 | 12 |
M16 | 17.5 | 17.5 | 17.77 | 17 | 17 | 17.18 | 18.5 | 18.5 | 19.02 | 14 |
M20 | 22 | 22 | 22.33 | 21 | 21 | 21.21 | 24 | 24 | 24.52 | 17.5 |
M24 | 26 | 26 | 26.33 | 25 | 25 | 25.21 | 28 | 28 | 28.52 | 21 |
M30 | 33 | 33 | 33.39 | 31 | 31 | 31.25 | 35 | 35 | 35.62 | 26.5 |
M36 | 39 | 39 | 39.39 | 37 | 37 | 37.25 | 42 | 42 | 42.62 | 32 |
M42 | 45 | 45 | 45.39 | 43 | 43 | 43.25 | 48 | 48 | 48.62 | 37 |
M48 | 52 | 52 | 52.46 | 50 | 50 | 50.25 | 56 | 56 | 56.74 | 43 |
M56 | 62 | 62 | 62.46 | 58 | 58 | 58.3 | 66 | 66 | 66.74 | 51 |
M64 | 70 | 70 | 70.46 | 66 | 66 | 66.3 | 74 | 74 | 74.74 | 57 |
M72 | 78 | 78 | 78.46 | 74 | 74 | 74.3 | 82 | 82 | 82.87 | 64 |
M80 | 86 | 86 | 86.54 | 82 | 82 | 82.35 | 91 | 91 | 91.87 | 71 |
M90 | 96 | 96 | 96.54 | 93 | 93 | 93.35 | 101 | 101 | 101.87 | 80 |
M100 | 107 | 107 | 107.54 | 104 | 104 | 104.35 | 112 | 112 | 112.87 | 89 |
Imperial Clearance Hole Chart In inches (with Tap Drill) | |||||||||||
---|---|---|---|---|---|---|---|---|---|---|---|
Nominal Screw Size | Fit Class – Normal | Fit Class – Close | Fit Class – Loose | Tap Drill | |||||||
Nominal Drill Size | Min. Hole Diameter | Max. Hole Diameter | Nominal Drill Size | Min. Hole Diameter | Max. Hole Diameter | Nominal Drill Size | Min. Hole Diameter | Max. Hole Diameter | Drill Size | Decimal Equivalent | |
#0 | #48 | 0.076 | 0.082 | #51 | 0.067 | 0.071 | 3/32 | 0.094 | 0.104 | 3/64 | 0.0469 |
#1 | #43 | 0.089 | 0.095 | #46 | 0.081 | 0.085 | #37 | 0.104 | 0.114 | 53 | 0.0595 |
#2 | #38 | 0.102 | 0.108 | 3/32 | 0.094 | 0.098 | #32 | 0.116 | 0.126 | 50 | 0.0700 |
#3 | #32 | 0.116 | 0.122 | #36 | 0.106 | 0.110 | #30 | 0.128 | 0.140 | 47 | 0.0785 |
#4 | #30 | 0.128 | 0.135 | #31 | 0.120 | 0.124 | #27 | 0.144 | 0.156 | 43 | 0.0890 |
#5 | 5/32 | 0.156 | 0.163 | 9/64 | 0.141 | 0.146 | 11/64 | 0.172 | 0.184 | 38 | 0.1015 |
#6 | #18 | 0.170 | 0.177 | #23 | 0.154 | 0.159 | #13 | 0.185 | 0.197 | 36 | 0.1065 |
#8 | #9 | 0.190 | 0.203 | #15 | 0.180 | 0.185 | #3 | 0.213 | 0.225 | 29 | 0.1360 |
#10 | #2 | 0.221 | 0.228 | #5 | 0.206 | 0.211 | B | 0.238 | 0.250 | 21 | 0.1590 |
1/4 | 9/32 | 0.281 | 0.290 | 17/64 | 0.266 | 0.272 | 19/64 | 0.297 | 0.311 | F | 0.2570 |
5/16 | 11/32 | 0.344 | 0.354 | 21/64 | 0.328 | 0.334 | 23/64 | 0.359 | 0.373 | F | 0.2570 |
3/8 | 13/32 | 0.406 | 0.416 | 25/64 | 0.391 | 0.397 | 27/64 | 0.422 | 0.438 | Q | 0.3320 |
7/16 | 15/32 | 0.469 | 0.479 | 29/64 | 0.453 | 0.460 | 31/64 | 0.484 | 0.500 | U | 0.3680 |
1/2 | 9/16 | 0.562 | 0.572 | 17/32 | 0.531 | 0.538 | 39/64 | 0.609 | 0.625 | 29/64 | 0.4531 |
5/8 | 11/16 | 0.688 | 0.698 | 21/32 | 0.656 | 0.663 | 47/64 | 0.734 | 0.754 | 37/64 | 0.5781 |
3/4 | 13/16 | 0.812 | 0.824 | 25/32 | 0.781 | 0.789 | 29/32 | 0.906 | 0.926 | 11/16 | 0.6875 |
7/8 | 15/16 | 0.938 | 0.950 | 29/32 | 0.906 | 0.914 | 1-1/32 | 1.031 | 1.051 | 53/64 | 0.8281 |
1 | 1-3/32 | 1.094 | 1.106 | 1-1/32 | 1.031 | 1.039 | 1-5/32 | 1.156 | 1.181 | 59/64 | 0.9219 |
1-1/8 | 1-7/32 | 1.219 | 1.235 | 1-5/32 | 1.156 | 1.164 | 1-5/16 | 1.312 | 1.337 | 1-1/16 | 1.0625 |
1-1/4 | 1-11/32 | 1.344 | 1.360 | 1-9/16 | 1.281 | 1.291 | 1-7/16 | 1.438 | 1.463 | 1-5/32 | 1.1562 |
1-3/8 | 1-1/2 | 1.500 | 1.516 | 1-7/16 | 1.438 | 1.448 | 1-39/64 | 1.609 | 1.634 | 1-1/4 | 1.2500 |
1-1/2 | 1-5/8 | 1.625 | 1.641 | 1-9/16 | 1.562 | 1.572 | 1-47/64 | 1.734 | 1.759 | 1-11/32 | 1.3438 |
5. How To Calculate Clearance Hole Diameter & Dimensions?
When designing assemblies with bolts and screws, especially in precision applications using GD&T positional tolerancing, it’s important to calculate clearance hole diameters instead of relying solely on standard “close” or “free” fit tables. Custom calculation ensures that, even in worst-case machining scenarios, your parts will always assemble interference-free.
Key Parameters to Know
Before beginning the calculation, gather these five values from your design:
- F: Maximum diameter of the fastener (bolt or screw)
- T₁: Positional tolerance for the clearance holes
- T₂: Positional tolerance for the threaded holes
- D: Minimum thread depth (for blind holes)
- P: Maximum length of the clearance hole (often the thickness of the part)
Step 1: Calculate the Minimum Clearance Hole Diameter (Hmin)
Use the following formula:
Hmin = F + T₁ + T₂ × (1 + 2P/D)
Example Calculation:
Given:
- F = 0.250 in (¼” fastener)
- T₁ = 0.007 in (clearance hole positional tolerance)
- T₂ = 0.014 in (threaded hole positional tolerance)
- P = 0.755 in (maximum part thickness)
- D = 0.500 in (minimum thread depth)
Plug into the formula:
Hmin = 0.250 + 0.007 + 0.014 × [1 + 2 × (0.755 / 0.500)]
= 0.250 + 0.007 + 0.014 × (1 + 3.02)
= 0.250 + 0.007 + 0.05628
= 0.31328
Note: Always round up the 4th decimal place (here, to 0.3133″) to guarantee you avoid any possible interference during assembly.
Step 2: Apply Size Tolerance
Choose a size tolerance based on the calculated minimum hole diameter and a suitable manufacturing tolerance table.
For example, if your Hmin is 0.3133″, and referring to the “Low Cost Drill Tolerance” chart:
- For diameters 0.201–0.400″, the recommended tolerance is +0.007/-0.002.
Step 3: Calculate the Nominal Clearance Hole Diameter (Hnom)
Calculate the nominal value by adding the absolute value of the lower tolerance to your minimum diameter:
Hnom = Hmin + |Lower Tol.|
= 0.3133 + 0.002
= 0.3153
This is your design value for the clearance hole diameter.
However, since standard drill bits come in set sizes, select the next larger standard drill bit. For this example, the next size up is a Letter “O” drill bit at 0.316″. This is what you should specify on your drawing as the practical clearance hole size.
6. How To Drill a Clearance Hole?
Clearance holes comprise large portions of the features that require machining. They can be created on lathes, drill presses, milling machines, or special-purpose machines such as a gun drill. They can be clearance holes with loose tolerances positional holes with relatively tight tolerances or bearing holes into which objects are often forced. Since holes serve a wide variety of functions, a large assortment of tooling has been created to properly machine them. Bolt clearance and tapped holes such as these are often made with job or length drills.
Due to the fact that these drills tend to wander as they work their way through the part, the hole should be started with a center or spot drill. Both spot drills and center drills are short rigid tools that when used correctly provide an excellent starting hole that minimizes the wandering of job or length drills. Spot drills are typically preferred over centre drills because when used correctly they are capable of leaving the desired chamfer at the top of the hole.
Stub drills, on the other hand, do not require a starting hole; they are short rigid drills designed to minimize wandering when drilling shallow holes up to two and a half times the drill diameter length. Clearance and tapped holes are typically created by spot drilling followed by drilling with the job or length drill, or in the case of short holes, a stub drill may be used.
If you are using a tap and clearance drill chart, first determine the screw size that you are going to utilize in your design. For example, if you need a clearance hole for a 1/4 inch fastener, you can use the drill size F for a close fit or drill size H for a free fit. This chart gives you all the information you need to know how to drill holes that are going to be tapped or holes that are going to be used as through holes or clearance holes so that your fastener can pass through the hole.