The term “automobile die” is used to refer to any die used in the production of an automobile. For instance, an injection mold, a stamping mold, a forging mold, a casting wax mold, a glass mold, and so on. The car’s outside body is the first thing that comes to mind while discussing automobiles. Hence, the body is the defining component of a vehicle. The outside of the automobile stands for the car’s overall aesthetic. Automobile die, in this restricted meaning, refers to the die used to punch all stamping components of the vehicle body. It’s also known as a “die for stamping vehicle bodies.” Flanging die for the top cover, plate forming die for the beam stiffener, etc. We are talking about a brief history and overview of their classification and production of automobile molds.
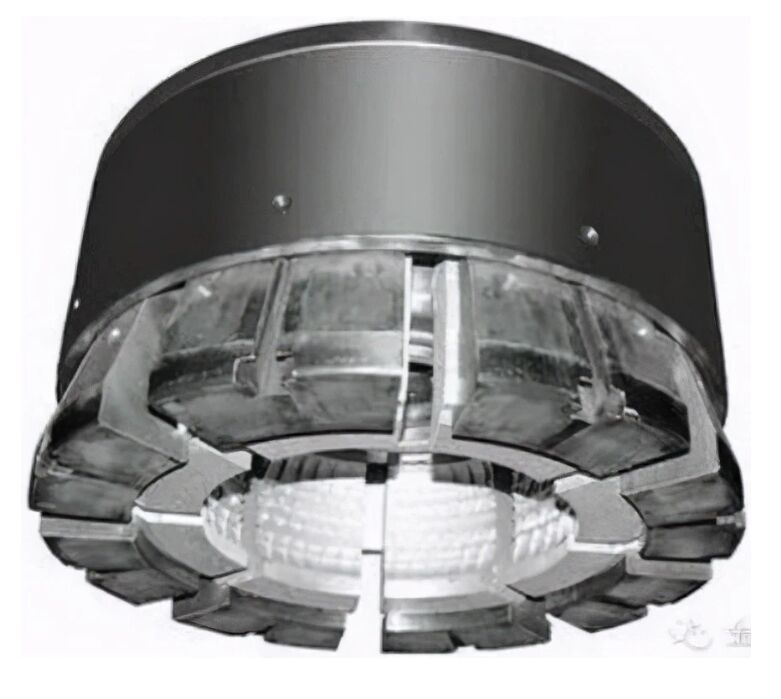
The Plastics Mold Used in Automobiles
Automotive plastic molds may be categorized in a number of ways depending on how the plastic components will be formed and processed, such as the following:
To create an injection mold
There is a similar term for injection mold. When making this mold, the plastic raw ingredients are heated in the injection machine’s barrel. Melting the plastic by applying heat. Through the injection machine’s nozzle and gating mechanism, the material is forced into the mold cavity. By controlling the temperature, maintaining the pressure, cooling, and solidifying the plastic in the mold cavity, a desired shape may be achieved. Injection molding is superior to other methods for producing complicated plastic components because of the heating and pressurizing device’s multi-stage involvement. As a result, injection molding is often used for plastic components, and injection molds make up more than half of all plastic molding molds. Injection machines were originally developed for molding thermoplastics, but they have since found increasing usage in the molding of thermosetting polymers.
Compression mode
Pressing die, or rubber pressing die, is another name for a compression die. Plastic raw materials are poured into the open mold chamber before the mold is closed to complete the molding process. When the plastic is heated and pressed together, it melts and fills the void with a certain amount of pressure. The plastic’s molecular structure underwent a chemical crosslinking process, causing the material to harden over time. Thermoset polymers are often employed in compression molds, and the molded plastic components are commonly used for the casing of electrical switches and other needs.
Mode de transfert
Pressure injection mold and extrusion mold are other names for the transfer mold. To create a product using this mold, plastic raw materials are first introduced into a preheated feeding chamber, where they are subjected to pressure from a pressure column. The plastic melts under high heat and pressure, flows into the mold cavity via the gating system, and eventually solidifies and forms as a result of a chemical crosslinking process. Transfer molding is often used to create intricate plastic pieces from thermosetting materials.
Forming tool for extrusion
The term “extrusion die” may also refer to the tool used in the extrusion process. Plastic pipes, bars, sheets, and so on may all be made reliably and repeatedly using the same mold. The extruder’s heating and pressurizing system is identical to that of an injection machine. Continual molded plastic pieces are efficiently created while molten plastic flows through the die head.
Vacuum forming molds, compressed air molds, blow molding molds, low foaming plastic molds, etc. are only a few more examples of plastic molds.
Vehicle bodies’ stamping components may be broken down into three broad categories: covering components, beam frame components, and general stamping components. Panels for cars are the stamping sections that best convey the car’s visual features. This means that “automotive panel stamping die” is the more accurate term for a more specialized kind of automobile die. The term “die” is used to describe the tool used to create automotive upholstery. Cutting dies for cutting the outer panel and punching the interior panel of a front door are only two examples.
Stamping dies for automobiles are categorized in
Stamping is used for more than just the car’s shell. The term “automobile stamping dies” is used to describe the molds used to produce metal stampings for car components. In conclusion:
-Automotive tooling, or “automotive die,” refers to the molds used to create various car components.
-All of the automotive stamping pieces are punched using the car stamping die.
-Each and every stamping component of a car body is punched using the automotive body stamping die.
-All of the covering components for a vehicle’s body are punched from a single die called a stamping die.
Tire deterioration caused by a fungus
Injection mold used for vulcanizing and shaping tires of several sizes and styles.
Molds for automotive tires, categorized into three types
The pattern ring, mold sleeve, and upper and lower side plates make up the flexible die.
Differentiate between mobile dies with a conical surface and those with an inclined plane.
Upper and lower molds make up the two halves of the mold.
The benefits of high-speed machining technology include:
High-speed cutting reduces the time it takes to complete a task.
Automobile dies are machined using high speed machining, which has a cutting speed around 10 times faster than traditional machining. The processing of car dies is steady and impact-free because the excitation frequency of the spindle of a high-speed machine tool is much beyond the natural frequency range of the “machine tool workpiece” system.
The high-speed cutting’s effective production rate
Using a high-speed machining center or high-speed milling machine, “One Pass Machining” allows the rough and finish machining of the mold surface and the machining of other components of the automotive mold to be finished in a single clamping of the workpiece. Increased productivity in the creation of vehicle molds is attributed in large part to the use of high-speed machining technologies.
High-velocity machining yields a smooth, precise surface.
Excellent speed cutting may get high surface quality and even remove the procedure of bench worker finishing because of the very tiny step distance and cutting depth.
Streamline administrative processes
Only before quenching is it possible to mill using conventional methods; after quenching, any distortion must be trimmed by hand or corrected by electric machining. High-velocity cutting is now possible, and case hardening due to electrical machining is no longer an issue. To further minimize production time, high-speed machining uses smaller-diameter tools to produce smaller fillet radii and mold details than conventional machining methods need.
Auto dies may be repaired faster using high-speed cutting.
In order to lengthen the life of a vehicle, it is typically necessary to have the engine, transmission, and other components fixed many times. High-velocity cutting allows for quicker job completion and produces the same machining result as grinding or milling, but with less wear and tear on the material. Not only can the original NC software be utilized, but it can be accurate without any re-programming.
The complicated geometries of hard vehicle dies may be machined using high speed machining.
The high-speed cutting mechanism demonstrates that high-speed cutting significantly reduces the cutting force required for the same level of cutting, making the operation much more manageable. Cutting materials with a high strength and hardness at high speeds offers several benefits. Automobile dies, despite their complexity and hardness, are no match for this machine.