Applications of Laser Cladding in Mould Manufacturing, Repair, and Maintenance | Diecasting-mould
Laser cladding is an advanced laser surface modification technology and the additive metal deposition process plays a significant role in mold making, repair, and maintenance. Follow us to understand the laser cladding process with its definition, benefits, and application.
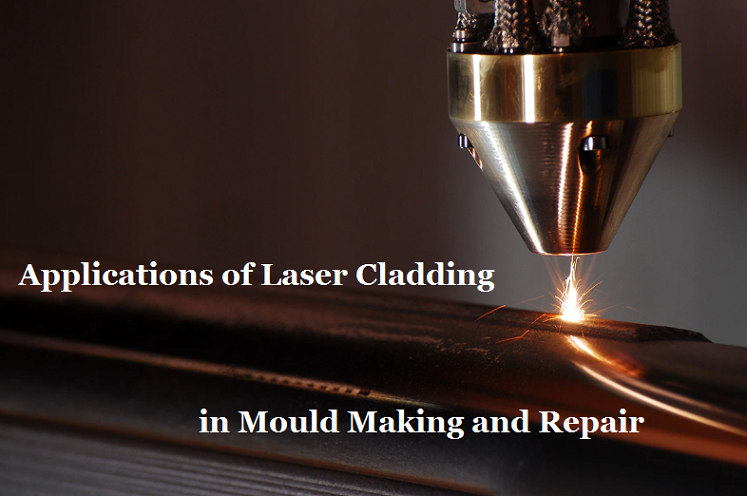
What is Laser Cladding?
Laser cladding including wire cladding and powder cladding, is a weld build-up process and complementing coating technology to thermal spray. Laser cladding uses laser energy as a heat source to melt the material to be welded, the laser beam creates a molten pool at the surface of the component, then weld or add the laser coating material onto the component. The laser cladding technology allows the use of the cheap substrate, while the product also can get greater performance and improved properties such as higher resistance to corrosion, oxidation, wear, and high-temperature fatigue strength, through the welding of special material on the surface of the substrate.
Advantages of Laser Cladding
Laser cladding technology is a new surface modification technology. It has the advantages of low dilution ratio, small heat-affected zone, metallurgical bonding with the base surface, small distortion ratio of cladding parts, and easy to realize automation.
1) The results show that the heat-affected zone is small, the deformation of the workpiece is small, and the cladding yield is high.
2) Low dilution ratio of the cladding layer, small melting amount of substrate, and low dilution rate of the cladding layer.
3) Because of its fine grain size and dense structure, the physical and chemical properties of the layer are relatively good (such as relatively high hardness, good wear resistance, and corrosion resistance).
4) The coating is well bonded with the substrate and the cladding quality is stable.
5) It is suitable for cladding with many materials and large variation of particle size and content.
6) The laser cladding process is easy to realize automatic production.
Applications of Laser Cladding in Mould Manufacturing, Repair and Maintenance
The application of laser technology to mould surface treatment can greatly improve the hardness, wear resistance, corrosion resistance, fatigue resistance, and other mechanical properties of parts surface, and greatly improve the service life of materials. At the same time, it can also be used to repair and maintain the mold, saving a lot of costs.
1. Laser cladding process can be used to make a high-performance surface on a low-cost metal substrate, so as to save valuable and rare metal materials, improve the performance of the base material, and reduce energy consumption. It is very suitable for the remanufacturing of dies which are locally vulnerable to wear, impact, corrosion, and oxidation. For example, the development cycle of a complete set of automobile dies is generally requires one year, it’s expensive but there are only a few changes on the basis of the same mold. Therefore, the old dies can be remanufactured into new ones by using laser cladding technology, which can greatly shorten the development time of new vehicle molds, save a lot of costs in mold making, and produce significant economic benefits.
2. The application of high-energy laser pulse to remove the surface dirt generated on the mold in the die casting services is another application of laser cladding in the mold industry. There are two cleaning principles: one is to use the laser to heat the dirt to vaporize, or to expand instantly and be carried away by steam; the other is to generate splitting stress in the dirt layer under the action of high energy density and high-frequency pulse laser, which separates the dirt layer from the mold substrate. Compared with the traditional sandblasting cleaning method, laser cleaning has the advantages of fast cleaning speed, no damage to the mold surface, and online cleaning.
3. Use laser cladding to repair the old or damaged mold. In fact, the failure of dies is scrapped due to the wear and tear of surface materials, the processing cycle of metal dies is long and the processing cost is high. The service life of the die depends on its ability to resist wear and mechanical damage. Once the die is over worn or damaged, it must be repaired before it can be used again. A high power CO2 laser beam with constant power and metal powder flow is incident on the die surface at the same time. The metal melts to produce a molten pool, and then rapidly solidifies to form a metallurgical coating. This method generally uses a high-power CO2 laser as a heat source, which is suitable for the repair of molds with large volume and wear area, as well as the repair of large workpieces such as steel rolls.