Application Of Nitriding Technology in Aluminum Alloy Die Casting
The consumption of aluminum alloy die-casting mold in aluminum alloy die-casting production is an important factor affecting the cost. The alarm red light of die-casting mold consumption in advanced industrial countries is 5% of the GDP. There are many die-casting factories whose consumption of die casting mold is higher than that of this line, so reducing the cost of die-casting mold is an urgent problem to be solved to reduce the production cost of aluminum alloy die casting.
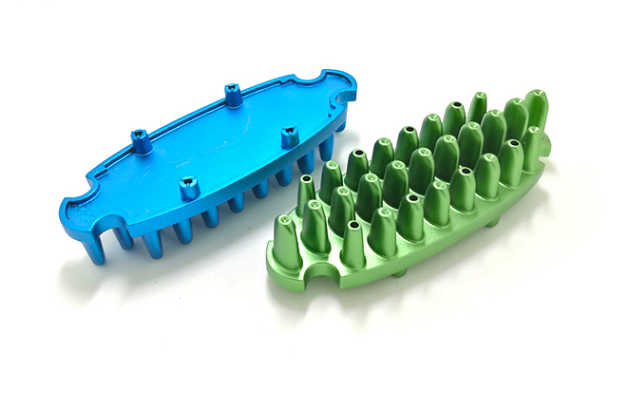
Application Of Nitriding Technology in Aluminum Alloy Die Casting
Accurate selection of die casting die materials, good heat treatment and good surface nitriding treatment are important means to improve the precision of die casting die. In order to effectively improve the service life of die casting mold, we developed and manufactured a new nitriding furnace which can control the nitriding quality factors by using various technologies at home and abroad, and debugged the nitriding process. After more than half a year of debugging, we can accurately control the compound layer, pulse structure, reasonable nitride layer hardness gradient and reasonable sub surface layer hardness of the nitride layer on the surface of the hot forging die, and meet the quality requirements of the nitride layer we designed. At the same time, we also carry out vulcanization, oxidation and other tests to further improve the service life, which will be applied to production.
Failure Mode of Die Casting Mold
The main failure form of surface nitriding die casting die is abrasive wear. The wear process is: compound layer rupture → hard particles → vein structure cracking → block falling → matrix scratch → repeated ploughing → cutting furrow.
Functions of Several Nitriding Furnaces
1. Nitrogen based atmosphere ternary gas nitriding furnace (Japan) this technology has the advantages of reliable product quality, good economy, good safety, no industrial pollution, shortening nitriding time and so on. It adopts common control system, which is difficult to control the quality factors of nitriding layer. This paper participated in the bit nitriding test in Japan. Because it is difficult to control the emergence of compound layer, only 30 min nitriding was done, which can improve the service life of the bit by about 30%. If the compound layer can be controlled, more service life can be improved.
2. The characteristic of the cathode ion screen nitriding furnace is that a separate cathode is added to the conventional ion nitriding furnace. The working principle is to convert the direct impact of ions on the metal surface into gaseous ions with the cathode screen, which gives full play to the advantages of gas nitriding and ion nitriding, and overcomes the problems that the microporous narrow gap of ion nitriding cannot be nitrided, the shape of workpiece The influence of size on nitriding (the nitriding quality of different workpieces cannot be controlled), and the problem of ion impact surface coarsening (surface coarsening is the factor of abrasive wear).
3. A new type of nitriding furnace has been developed. Combined with the advantages and disadvantages of nitriding furnaces at home and abroad, a new type of nitriding furnace has been developed, which adopts (NH3 + N2 + CO2) ternary gas nitriding; Use pt-500 control system, ammonia cracker, hydrogen probe and oxygen probe to accurately control the nitrogen potential in the furnace; Low vacuum protection and rapid cooling technology.