Analysis Of Porosity Defects In Die Casting Shells | Diecasting-Mould
Die casting is a high efficiency and low cutting metal forming precision casting method that is developing rapidly in China. Compared with other casting methods, it is not only environmentally friendly, but also has advantages of short production process, simple procedures, high production rates of die castings, high precision, low surface roughness and less machining, which is widely used in the production of parts in various industries. However, because die casting has characteristics of high speed and high pressure, casting defects such as porosity and shrinkage porosity will inevitably occur in die castings. It is significant to study how to control the porosity, location and quantity inside the die casting. Taking a certain type of aluminum alloy left case as an example to analyze and solve the gas porosity defect in the bearing mounting hole position in this article.
Analysis Of Porosity Defects In Die Casting Shells
1. Die casting structure and technical requirements
A certain type of aluminum alloy left case’s external dimensions are 423x298x246mm, the maximum wall thickness is 21mm, the minimum wall thickness is 4.0mm and the product weight is 6.43kg. The wall thickness of the bearing mounting hole position in this picture is thick, which is very different from the surrounding wall thickness, and is of a ring shape. Gas entrainment and turbulence are prone to occur when the molten aluminum is filled, which leads to the occurrence of a lot of gas holes and shrinkage cavities on the thick part. One of the most important quality requirements of the product is to place the case in the sink, clamp and inflate the case by the air pressure device, making the inside of the box reach 0.1 to 0.2Mpa. Keep the pressure for 10 seconds after the inflation is completed, and there is no leakage at the case.
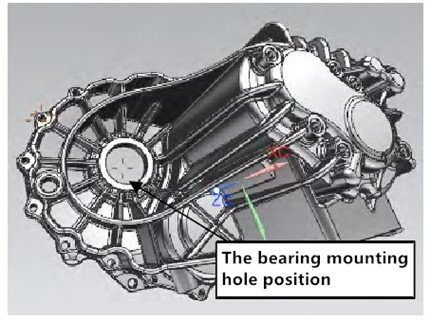
2. Defects and cause analysis of die castings
2.1 Die casting defects
The left case uses high-pressure casting, and the high speed and high pressure of the die casting process make the aluminum liquid prone to gas entrainment and turbulence when the cavity is filled, resulting in gas porosity often being inside the die casting. In the small batch trial production of aluminum alloy left cases, it was found that there were a large number of gas porosity defects in the bearing mounting hole position through X-ray non destructive testing. The gas porosity defect will be inside the die casting, which can not be observed with the naked eye, but it will be exposed after machining The qualified rate of produced die castings is lower.
2.2 Cause analysis
The main reasons for the porosity defects of die casting shells are as the following:
Firstly, because the wall thickness of the bearing mounting hole of the die casting is thick, and the wall thickness varies greatly with ring shapes, which is difficult for process control. Secondly, because of the unreasonable design of the mold gating system and slag bag, the inlet direction and distribution of the designed gating affect the exhaust effect at the position of the bearing installation hole. The molten aluminum firstly fills the slag bag when filling, which leads to the designed slag at the position not playing a good role in collecting slag and gas. Thirdly, the speed of the inner gate is too high, and turbulence is generated. The fast position is set improperly; the pouring temperature is high, and the specific pressure is small. All of these result in generating gas porosity.
3. Process measures
3.1 Modifying the mold gating system and slag bag
Since the die castings have their own characteristics, they are very practical and empirical. Must try to ensure that the liquid flow fills along the wall at the inlet direction of the molten aluminum to facilitate exhaust. The distribution being more orderly filled and the gas being discharged should be considered for the distribution method of the runner. Therefore, the mold for the left case was modified. A sprue was added to the fixed mold of the left case mold of the casting system (see the below picture), which increased the cross-sectional area of the inner gate and reduced the filling speed of the inner gate. The molten aluminum can be filled along the molding wall, and the amount of molten aluminum filling the position of the bearing installation hole of the die casting is increased.
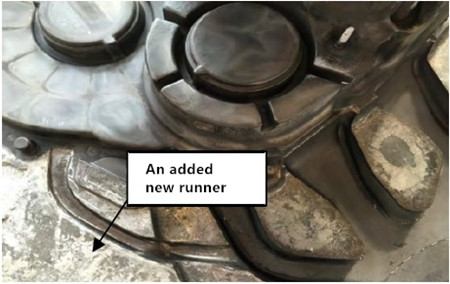
By modifying the slag bag at the position of the bearing installation hole of the left case, the volume of the slag bag is increased, so that the slag bag can contain the gas wrapped by the molten aluminum when filling the position of the bearing installation hole, reducing the appearance of gas holes on the position.
3.2 Mold flow analysis
Through computer mold flow analysis, it is found that after modifying the mold gating system and the slag bag, the aluminum water first fills annular holes bearing installation of the left case movable mold (see below picture), then fills the slag bag after joining. The gas is discharged to the slag bag. At the same time, since the molten aluminum arrives at the slag bag at the end, its solidification is slower than that of around the annular hole of the bearing installation, which is beneficial for gas collection and slag collection.
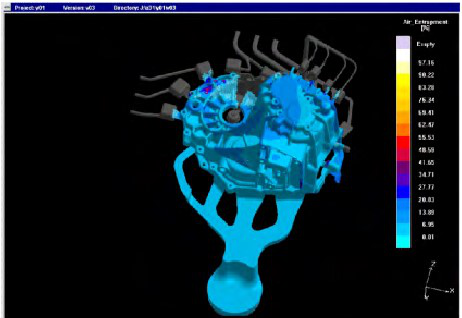
3.3 Controlling process parameters
Aiming for the gating system of this product, in order to prevent the gas holes on the machined surface at the far end of the gate, the slow and fast switching points are adjusted to reduce the pouring temperature and increase the boost pressure for control. Practice has proved that the second fast position is set at 485mm compared with the original second fast position 470mm, which improves the fullness of the pressure chamber. Maintain the spoon to make the soup volume stable. The boosting flow rate was increased from 60% to 80%, which satisfied the effect of pressure boost and feeding after the rapid completion. Adjust the molten aluminum pouring temperature from 650°C to 630°C, and the gas porosity defect has been effectively controlled.
4. Conclusion
(1) Modifying the gating system, increasing the cross-sectional area of the inner runner and modifying the size of the slag bag can effectively solve the problem of gas porosity defects in the die casting production process.
(2) Taking measures such as appropriate adjustment of slow and fast switching points, increasing boost pressure and lowering pouring temperature can effectively solve the generation of die casting aluminum alloy shells gas porosity in similar products.
(3) Effective control of gas porosity in die castings during the production process, improving product quality and saving production costs are of important reference to production practice
If you are looking for some products produced by die casting service for your project, Diecasting-Mould can be your best partner! We offer best ISO9001:2000 certified die casting products at affordable prices. We are capable to complete mass production of custom die casting products in high speed and on-time delivery. Contact us, send your sample or drawings to us and get the professional quotation immediately!