Aluminum castings have a high metal application rate and lower processing equipment and casting costs because to their precise dimensions and high-shine surfaces, which allow them to be utilized immediately after mechanical processing. Metal and assembly time may be reduced when die casting is used in conjunction with other metals or non-metallic components. Though there are numerous benefits to using aluminum castings, there are also certain flaws that must be addressed. For instance, the standard die casting technique is used in die casting because of the rapidity with which liquid metal fills the cavity and the inherent instability of the process. Blowholes are simple to create in the castings, and the heat treatment can’t be halted. Die casting presents more of a challenge when the casting in question has a complicated concave. Alloys with a high melting point, like copper or ferrous metal, have a short die casting life and are not practical for single-unit production. As a result of high formation costs, high consumption rates, and excellent consumption rates of die-casting machines, small batch consumption is uneconomical.
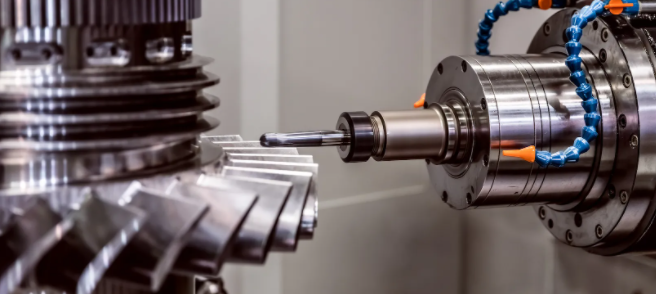
For die cavity dimension inspection, casting scribing, and machining, the datum plane will be chosen as the central factor. The casting’s end face, end face, inner hole, or outer circle may all serve as datum planes. Design, processing, and casting professionals may all agree on the same datum plane. The following guidelines should be used as a general rule when deciding on a datum plane:
1. The investment casting datum plane is typically a non-machining surface. When choosing a machining surface, the one with the smallest machining allowance should be used.
2. The datum plane is the plane between the plane to be machined and the plane with accuracy criteria; the design datum and processing datum of the component should overlap as much as feasible.
3. As a rule of thumb, three datum planes are chosen (two datum planes are used for rotating components) and the same datum plane is used for scribing and processing to ensure a full six degrees of freedom.
There is a vast variety of uses for die casting. Casting aluminum is a metal-forming technique. It’s the key to getting by with fewer or even zero chips. It’s getting a lot of usage and improving quickly. Die casting alloy has progressed from being used only for nonferrous metals like zinc, aluminum, magnesium, and copper to increasingly include ferrous metals like cast iron and steel. The strength of the die casting machine determines the dimensions and mass of the resulting castings. The casting’s form and size may vary from a few millimeters to half a meter; the casting’s weight can vary from a few grams to tens of kilos, depending on the machine’s power. There are now many more industries that use die castings than only the automotive and instrument manufacturing sectors. These include the agricultural equipment, machine tool, electrical, computer, clock, camera, and everyday hardware industries. New technologies, such as vacuum die casting, oxygenated die casting, precise speed die casting, and the use of soluble cores, have also been introduced in the field of die casting.
In what conditions should aluminum castings be kept?
1. Sand cast aluminum castings must be kept in a climate-controlled, dry, and noncorrosive inventory environment; exposure to moisture from rain must be absolutely avoided at all costs.
2. There can be no chemical interaction between the sand cast aluminum castings and anything else. When sand cast aluminum castings come into touch with other chemicals, the other chemicals will react with the sand cast aluminum castings, damaging the sand cast aluminum castings.
3. Every single aluminum casting made from sand is unique in its own right. In order to ensure that the zinc alloy sand cast aluminum casting goods are not damaged during placement, it is recommended to create a unique blister disk for each casting, based on its form.
4. It’s an active metal, hence it’s number four on the list. It is simple to come into touch with and oxidize when the temperature is right. Therefore, care must be taken to maintain a consistent temperature and keep the castings out of direct sunlight while storing zinc alloy sand cast aluminum.
5. To prevent “blasting” during melting, which might injure people or destroy equipment, it is important to dry the raw alloy ingot of the cast zinc alloy product before adding it.
There are three steps involved in the heat treatment process for aluminum castings: heating, heat retention, and cooling. Several variables, including heating rate, heating temperature, holding duration, cooling rate, and heat treatment cycle, may characterize the whole procedure. Among the many requirements for a successful heat treatment, temperature ranks high. The quality of aluminum castings will decrease, if not be scrapped, if the temperature measurement is inaccurate, since this will result in improper implementation of the heat treatment process specification. The key to a successful heat treatment procedure and the most important element influencing distortion is accurate temperature monitoring and control. It is also crucial to note that the cooling process after quenching may have a significant impact on the distortion of aluminum castings. After undergoing a heat treatment, metal always cools from the inside out, with the thinner sections cooling more quickly than the thicker ones. In order to minimize distortion and cracking in the transition zone as a result of stress concentration, it is important that the section of the component be uniform in thickness and that the workpiece thickness difference be as small as possible to fulfill production demands. After heat treatment, the casting in aluminum must undergo further processing. According to the casting’s deformation rule, an anti-deformation and pre-expansion hole at the shrinkage end must be used to increase the deformation qualification rate after quenching.