Sandblasting and anodizing are two surface treatments that can be applied on aluminum and aluminum alloys, here let’s talk about what are aluminum sandblasting and aluminum anodizing, as well as the difference between them.
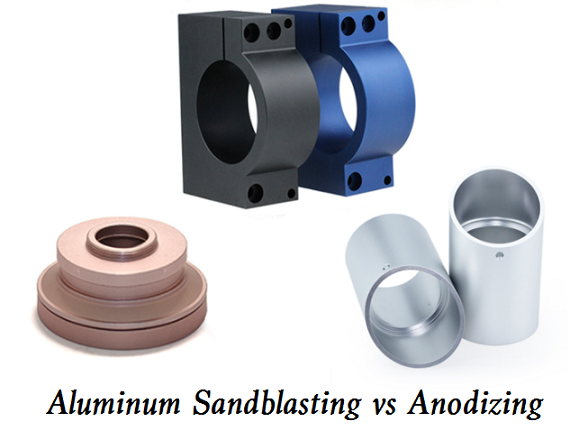
What is Aluminum Sandblasting?
Sandblasting uses compressed air as the power to form a high-speed jet beam to spray the materials to the surface of the workpiece to be treated at a high speed so that the appearance or shape of the external surface of the workpiece surface changes. Due to the impact and cutting effect of the abrasive on the surface of the workpiece, the workpiece surface can obtain a certain degree of cleanliness and different roughness, so that the mechanical properties of the workpiece surface can be improved, Therefore, the fatigue resistance of the workpiece is improved, the adhesion between the workpiece and the coating is increased, the durability of the coating is extended, and it is also conducive to the leveling and decoration of the coating. Aluminum sandblasting uses high-speed compressed air to spray carborundum on the aluminum surface so that the metal surface will produce tiny depressions. These small pits are uniform and delicate, which can not be seen with the naked eye, but the aluminum profile surface has a sanding effect.
What is Aluminum Anodizing?
Anodizing refers to the process in which aluminum and its alloys form a layer of oxide film on aluminum products (anodes) under the action of external current under the corresponding electrolyte and specific process conditions. It has rich colors, beautiful colors, good electrical insulation, hardness, wear resistance, and high corrosion resistance. The basic principle is that under the action of the electrode and electrolyte, the aluminum ions on the surface will be decomposed into the electrolyte and mixed with the pigment ions, and then the electrode will be reversed to make the aluminum ions and pigment ions reattach to the surface of the aluminum piece so that the oxide film with uniform color and strong adhesion can be plated.
Aluminum Sandblasting vs Anodizing, What’s the Difference
1. Principle
Sandblasting is a process of cleaning and roughening the substrate surface by using the impact of high-speed sand flow. The compressed air is used as the power to form a high-speed jet beam to jet the materials (copper ore, quartz sand, carborundum, iron sand, Hainan sand) to the surface of the workpiece to be treated at a high speed so that the appearance or shape of the external surface of the workpiece surface changes, which can increase the roughness of the aluminum surface. Anodizing is a process of electrolytic oxidation, in which metal or alloy parts are used as anodes to form oxide films on their surfaces by electrolysis.
2. Characteristics
Sandblasting is used to impact and cut the surface of the workpiece with the abrasive so that the surface of the workpiece can obtain a certain degree of cleanliness and different roughness, and the mechanical properties of the surface of the workpiece can be improved. Therefore, it improves the fatigue resistance of the workpiece, increases the adhesion between it and the coating, extends the durability of the coating, and is also conducive to the leveling and decoration of the coating. The sandblasting process makes the aluminum surface have the characteristics of moderate hardness, high bulk density, no free silicon dioxide, heavyweight, good toughness, and environmental protection. Anodic oxidation has protective, decorative, and insulating properties, which can improve adhesion with organic coatings and inorganic coatings. The metal oxide film changes the surface state and properties, such as surface coloring, improving corrosion resistance, enhancing wear resistance and hardness, and protecting the metal surface.
3. Applications
The purpose of sandblasting is that sandblasting before workpiece coating and workpiece bonding can remove all dirt on the surface of the workpiece, such as the rust scale, and establish a very important basic diagram on the surface of the workpiece. Cleaning and polishing sandblasting of the rough surface of castings and workpieces after heat treatment can remove all dirt on the surface of castings and forgings and workpieces after heat treatment. Burr cleaning and surface beautification sandblasting of machined parts can remove small burrs on the surface of workpieces. Aluminum surface sandblasting technology has been widely used, mainly in automobile manufacturing, the rail transit industry, machinery and equipment manufacturing, and other industrial fields. Anodizing is applicable to the anodizing treatment of non-ferrous metals or their alloys (such as aluminum, magnesium, and their alloys). This method is widely used in mechanical parts, aircraft and automobile parts, precision instruments and radio equipment, daily necessities, and architectural decoration.