The car body accounts for about 40% of the total vehicle mass. For the lightweight of the whole vehicle, the lightweight of the body plays a decisive role. Aluminum alloy is the primary lightweight material used in the automotive industry. What aluminum materials are used in the automotive industry and what auto parts are used by aluminum alloy? We’ll also talk about the advantages of aluminum for vehicles and automobiles.
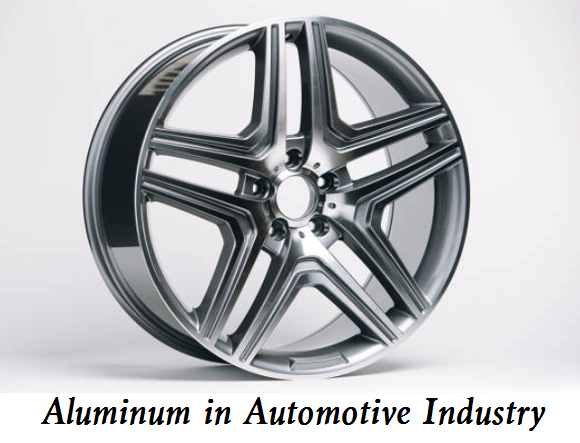
Advantages of Aluminum in the Automotive Industry
The automotive industry has very strict requirements for parts. Material safety is obviously the first priority. Many components must be ductile to absorb energy during impact, while other components must have the strength to maintain structural stiffness. The reason why aluminum alloy can play such an important role in automotive lightweight comes from its unique performance:
– The density of aluminum alloy is only 1/3 of that of steel. At the same time, aluminum can improve its strength through work hardening or heat treatment, so as to achieve high strength weight ratio;
– Aluminum alloy has good processability and is suitable for different production processes such as casting, extrusion, stamping, forging, and machining;
– Aluminum alloy can also be strengthened to different degrees by adding different alloy elements and heat treatment process similar to steel;
– Aluminum alloy surface is easy to form dense oxide film and has good corrosion resistance;
– In addition, the aluminum alloy also has good conductivity and thermal conductivity, and non-magnetic characteristics.
Aluminum Grades Used in Automotive Industry
The grades of aluminum alloys are divided into nine series from 1000 to 9000 according to the types and contents of non-aluminum elements.
Aluminum alloy materials for automobile bodies mainly include the 2000 series with the highest copper content and high hardness, the 5000 series mainly containing magnesium, also known as magnesium-aluminum alloy, 6000 series with high magnesium silicon content, good corrosion resistance, and oxidation resistance. Different series of aluminum alloy materials such as plates, profiles, pipes, and high-performance cast aluminum will be used in different stress parts of an automobile body.
– Frames: the part of the body with the greatest stress, which is made of 2000 series or 7000 series aluminum materials and can be strengthened by heat treatment.
– Outer panel: the secondary force-bearing part of the car body is made of 5000 series or 6000 series aluminum.
– Door: 5000 series or 6000 series aluminum.
– Floor: 5000 series or 6000 series aluminum.
– Casting: High-performance cast aluminum alloy can be strengthened by heat treatment.
Aluminum Castings and Other Aluminum Parts in Automotive Industry
6000 series aluminum alloy plates are usually made into outer panels of car bodies. They have high strength, can resist the large strain generated in the stamping process, and also have a certain baking hardening ability. The 5-series aluminum alloy is usually used as the interior panel and body structure, and its price advantage is higher than the 6-series aluminum alloy. However, 6000 series (Al-Mg-SI) and 7000 series (Al-Zn) aluminum alloys are often used for aluminum alloy extrusion or forging parts in lightweight automobiles. They are mainly used in engine support, body vertical and horizontal, body frame, seat frame, bumper beam, etc.
Aluminum alloy parts for automobile bodies mainly include cast aluminum connectors, covering parts (sheet stamping), extruded profile skeleton structural parts, hydroforming sheet covering parts, and pipe structural parts. Aluminum castings are manufactured to carry heavy loads, significantly reducing weight but also having high strength. These plates have complex geometric shapes, usually by vacuum die casting, which makes them have high strength. Aluminum castings also have high ductility, good welding performance, and high plasticity, ensuring high safety in case of collision. The aluminum alloy type of these castings is 5000 or 6000 series aluminum alloy. At present, aluminum castings are mainly used in the battery pack structure box of electric vehicles.