Aluminum Die Casting vs Magnesium Die Casting - Is Magnesium Better Than Aluminum?
Die casting is a method for high-volume production with different materials. One of the most important considerations in metal casting is the selection of material. In this article, let’s compare aluminum die casting vs magnesium. Is magnesium better than aluminum? Why aluminum castings are widely used for a long time?
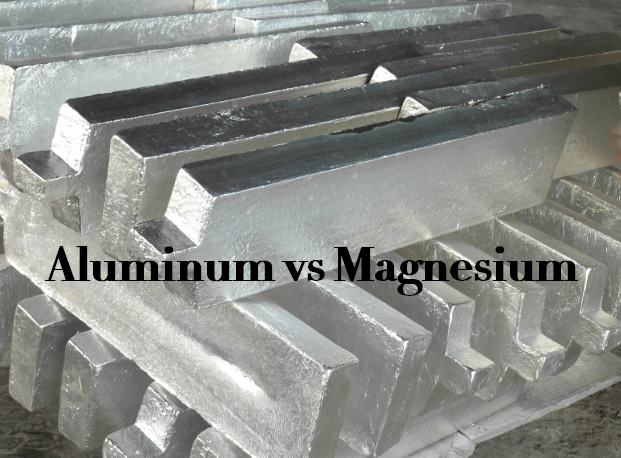
Aluminum Die Casting
Aluminum die casting is a type of pressure casting, using a pressure die casting machine with die casting mold to heat the aluminum to liquid and then pour the molten aluminum into the cavity, to get the aluminum die casting parts with certain shape and sizes.
Characteristics and Properties of Aluminum Alloy
The main alloying elements are copper, silicon, magnesium, zinc and manganese, also adding nickel, iron, titanium, chromium and lithium. Aluminum alloy has low density, high strength, which is close to or better than high-quality steel, good plasticity, and can be processed into various profiles, with excellent conductivity, thermal conductivity and corrosion resistance. It is widely used in various industries. Aluminum alloy is divided into two categories: cast aluminum alloy, used in as casting process; and wrought aluminum.
Advantages of Aluminum Die Casting
– Lightweight and durable
– Great corrosion resistance
– High thermal and electrical conductivity
– Good strength and hardness
– High dimensional stability for complex shapes and thin walls
– Retains strength at high temperatures
– Less expensive
– High utilization rate of material
– A longer die life
– Does not require as much finishing work as magnesium
Disadvantages of Aluminum Die Casting
– High viscosity of aluminum
– Take longer to solidify compared to magnesium alloys
Magnesium Die Casting
Pure magnesium can not be used as a structural material. The magnesium alloy formed by adding aluminum, zinc, lithium, manganese, zirconium and rare earth elements into pure magnesium has high strength. At present, the magnesium-aluminum alloy is the most widely used, mainly used in aviation, aerospace, transportation, chemical industry, rocket and other industrial sectors.
Characteristics and Properties of Magnesium Alloy
– Magnesium alloy is 30% lighter than aluminum alloy and 80% lighter than steel. Therefore, magnesium alloy has become an ideal material for parts manufacturing in automobile and portable electronic products.
– Magnesium alloy has an excellent strength to weight ratio in metal and plastic engineering materials.
– In good condition, the minimum wall thickness of magnesium alloy castings can reach 0.6 mm, which can not be achieved by plastics under the same strength. The die casting performance of aluminum alloy can be compared with that of magnesium alloy only when it is above 1.2-1.5mm. Magnesium alloy is easy to die cast, suitable for mass die casting production. In addition, the wear of magnesium casting mold is lower than that of aluminum.
– Magnesium has excellent shock absorption performance, which can absorb vibration and noise.
– Magnesium has good high rigidity and stress resistance.
– Magnesium alloy has good electromagnetic wave barrier function, suitable for the production of electronic products.
– Magnesium has good machinability.
– The affinity between magnesium alloy and mold steel is small, so it is not easy to adhere to the die.
Advantages of Magnesium Die Casting
– High productivity
– High precision
– Good surface quality
– Fine grain of casting
– Can be made to thin wall and complex structure die casting products
– Better at casting parts with thinner walls and tighter tolerances than aluminum.
Disadvantages of Magnesium Pressure Casting
– Due to the extremely high liquid filling speed and solidification speed, it is easy to produce embrittlement pores, the requirement for exhaust and cold material treatment are high.
– The casting should not be too thick, and the wall thickness can only be limited to a certain size.
– Cheap die casting magnesium alloy with limited mechanical properties.
– Limited types of die casting magnesium alloy can be used.
– Because of the small grain size, the creep resistance of the casting is poor.
– Creep-resistant magnesium alloys have poor castability and are expensive.
– Can’t be heat treated.
– Not suitable for welding.
Aluminum vs Magnesium Die Casting, Which One Should You Choose?
There is no big difference between aluminum alloy and magnesium alloy, but the aluminum alloy is slightly heavier. Aluminum alloy is one of the most common materials for die castings manufacturing, due to its lightweight, high dimensional stability for complex shapes and thin walls, smooth appearance, and good mechanical properties. However, its viscosity is relatively high. Moreover, the die cast aluminum alloy contains high content of Si, so it reacts with the solution directly when anodizing. So aluminum castings are not suitable to be anodized. When it comes to the cost factor, aluminum is the more budget choice. If you want to choose an aluminum alloy for metal casting, ADC 12 (A383) is a good choice as it has good fluidity and is easy to die-casting, and ADC 10 (A380), which is the most widely used cast aluminum.
Anodizing can be used for the magnesium castings, and the color is bright. Magnesium alloy die casting can be used to cast thin-walled and complex structure products. If you want extremely light castings, magnesium is what you should choose. Based on the characteristics of magnesium, it is more ideal when shock absorption performance, electromagnetic wave barrier function, high rigidity, and good machinability are required.