Advantages & Disadvantages Of Plating Process On Zinc Die Casting - Water Plating Vs Vacuum Plating
Both vacuum plating and water plating are used in the surface treatment of zinc alloy die casting parts. Zinc alloy die casting products generally adopt surface treatment, because the processed die casting products are more beautiful and wear-resistant. There are two plating methods for zinc alloy die casting parts, namely water plating and vacuum plating. The water plating process is suitable for zinc alloy die casting products, mainly for plating products in electroless plating bath. Vacuum ion plating, also known as vacuum coating, is suitable for zinc alloy die casting products. Due to the complex process, high requirements of environment and equipment, the unit price is more expensive than that of water and electricity plating. This article explains the advantages and disadvantages of plating process on zinc die casting and difference between water plating vs vacuum plating.
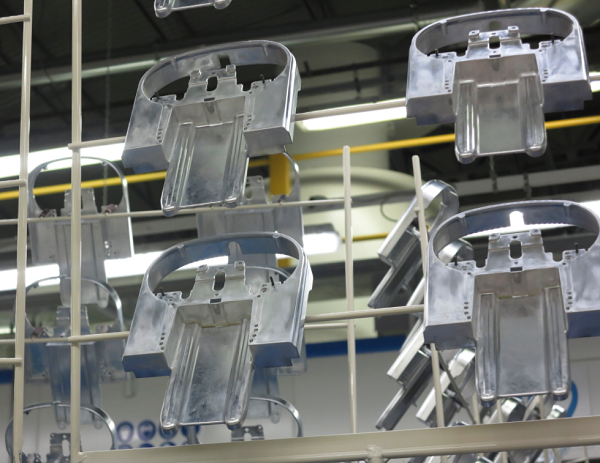
Advantages & Disadvantages Of Plating On Zinc Die Casting
The biggest difference between water plating and vacuum plating is the price. The price of vacuum plating is higher than that of water plating, and the process complexity of vacuum plating is also higher than that of water plating. The advantages and disadvantages of the two methods are briefly introduced.
1. If UV oil is used in the first vacuum plating, the adhesion of the treated zinc alloy die castings is very poor, and it is impossible to pass the test. Therefore, from this point, water plating process is better than vacuum plating! Therefore, vacuum plating is needed, and special spraying treatment must be carried out in the future, so the cost is very high.
2. The color of water coating is monotonous, generally only a few colors, such as white chrome and black lattice. However, vacuum plating is made from a variety of seven colors as it requires post-treatment.
3. The general plating material of water coating is “hexavalent chromium”, which is a kind of non environmental material.
Through the above analysis, you must have a certain concept of vacuum plating and water plating! Diecasting-mould is a professional manufacturer of zinc alloy die casting parts and aluminum alloy die casting parts. The company specializes in die casting industry for more than 10 years. The process from mold design to surface treatment is very mature, which effectively improves the die-casting parts.
Zinc Die Casting Plating Process
Product surface cleaning, de priming – spray primer – vacuum coating – spray finish – > baking finish – packaging. Vacuum plating can be divided into general vacuum plating, UV vacuum plating and special vacuum plating. The process includes evaporation, sputtering, gun color, etc.
Difference Between Water Plating and Vacuum Plating
Water plating process is relatively simple, and it does not need vacuum ion plating from equipment to environment, so it has been widely used. However, there is a weakness in water plating, only ABS material and ABS + PC material can be electroplated (the effect of this material plating is not very satisfactory). The temperature resistance of ABS is only 80 ° C, which limits its application. However, vacuum plating can reach about 200 ° C and can be used for plating parts used at high temperatures. PC materials, such as vents and tuyere rings, must withstand temperatures up to 130 ° C. In addition, high temperature resistant parts are generally required. The end of vacuum plating should be sprayed with a layer of UV oil to make the product surface glossy, high temperature resistant and ensure adhesion.
Advantages & Disadvantages of Vacuum Plating and Water Plating
1. Surface treatment: generally, before coating, the substrate (plated parts) should be pretreated by degreasing and dedusting to ensure that the coating parts are clean and dry, and to avoid defects such as pitting and poor adhesion of the bottom film. For special materials, such as PE (polyethylene), they should be modified to achieve the required coating effect.
2. Primer: when the primer is applied, it can be sprayed or impregnated according to the size, shape, structure of the coating parts, the specific conditions of the user’s equipment and the quality requirements of customers. Sz-97t can be applied with spraying method; sz-97, sz-97 + 1 and other oils can be applied with immersion coating method according to plating materials. View the applicable range of each product in the product display screen.
3. Primer drying: coating oil series is self-drying paint, the purpose of drying is to improve production efficiency. The drying temperature is usually 60-70 ° C for about 2 hours. The drying requirement is that the film is completely dry.
4. Coating: during coating, ensure that the vacuum degree of the coating machine meets the requirements, then heat the tungsten wire, and strictly control the heating time. At the same time, the quantity of metal (such as aluminum wire) used for coating should be mastered. Too little may cause the metal film to cover the substrate. Too much will affect the life of tungsten wire and the quality of coating.
5. Topcoat: generally, the purpose of coating is as follows:
A. Improve the water resistance, corrosion resistance and wear resistance of coated parts
B. It is possible to stain water stains.
If the plated parts do not need coloring, you can use 911, 911-1 Matt oil, 889 transparent oil, 910 Matt oil and other surface oil coatings according to customer requirements.
6. Drying of top coat: generally, the top coat is thinner than the bottom coat, and the drying temperature is lower, about 50-60 ℃. Baking time can be flexibly controlled according to the actual requirements of customers, and the final surface layer should be completely dry.
7. Water dyeing: if the coated parts need to be dyed with water, the baked and dried coated parts can be put into the dyeing tank, dyed with the required color, then washed and dried, and pay attention to dyeing. The water temperature is usually about 60-80 ℃, so the dyeing time should be controlled. The disadvantage of water dyeing is easy to fade, so the cost is low.