There are numerous types of aluminum alloys used in different manufacturing processes and industries, when it comes to cast aluminum, what are the differences between ADC12 aluminum, A380, and 6063?
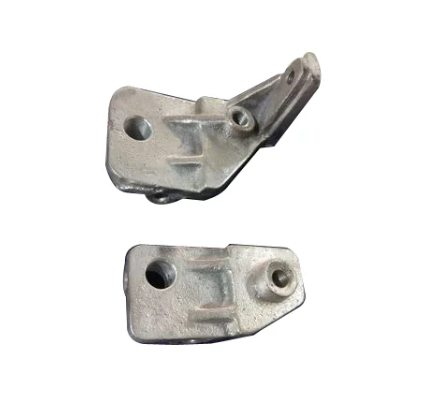
What is ADC12 Material Equivalent To?
ADC12 is an aluminum alloy that is equivalent to the American alloy designated as A383. It is a commonly used alloy in the die casting process. The ADC12 designation is based on the Japanese Industrial Standards (JIS) for aluminum alloys, while A383 is based on the Aluminum Association (AA) standards used in the United States. While ADC12 and A383 are considered equivalent in terms of their composition and general properties, slight differences may exist due to variations in specific manufacturing practices or regional standards.
Advantages of ADC12 Aluminum
1. Excellent Castability: ADC12 has excellent fluidity and castability, allowing for the production of intricate and complex shapes with high precision. It can fill molds with thin walls and intricate details, making it suitable for a wide range of casting applications.
2. High Strength: ADC12 offers good mechanical properties, including high strength and hardness. It provides a balance between strength and ductility, making it suitable for applications that require load-bearing capabilities and resistance to deformation.
3. Lightweight: Aluminum alloys, including ADC12, have low density, making them lightweight compared to many other metals. This property is beneficial in industries like automotive and aerospace, where lightweight components help improve fuel efficiency, reduce overall weight, and enhance performance.
4. Corrosion Resistance: ADC12 offers relatively good resistance to corrosion, making it suitable for applications exposed to moisture or certain chemicals. While additional coatings or treatments may be necessary for harsher environments, ADC12 exhibits adequate corrosion resistance in many typical operating conditions.
5. Thermal Conductivity: ADC12 has good thermal conductivity, enabling efficient heat dissipation. This property is advantageous in applications where effective cooling is essential to maintain optimal operating temperatures, such as in electronics and heat exchangers.
6. Machinability: ADC12 is known for its favorable machinability. It can be easily machined, drilled, and tapped to create precise features and dimensions required for specific applications.
7. Recyclability: As an aluminum alloy, ADC12 is highly recyclable. It can be melted and reused without significant loss in quality or performance, offering environmental sustainability and cost benefits.
ADC12 Aluminum vs A380 vs 6063, What Are the Differences
1. Chemical Composition:
ADC12: ADC12 aluminum alloy consists of a percentage of aluminum (around 90-92%), with silicon (9.6-12%), and smaller quantities of copper, magnesium, and other impurities.
A380: A380 aluminum alloy typically contains higher levels of aluminum (approximately 86-88%), along with copper (3-4%), silicon (8-9.5%), and smaller amounts of magnesium, iron, and other trace elements.
6063: 6063 aluminum alloy consists of approximately 98.9% aluminum, with silicon (0.2-0.6%) and smaller levels of iron, copper, manganese, magnesium, and other trace elements.
2. Mechanical Properties:
ADC12: ADC12 has slightly higher mechanical properties, especially greater hardness and a higher yield strength, compared to A380.
A380: A380 offers good strength and ductility, making it suitable for applications requiring structural components with increased load-bearing capabilities.
6063: 6063 has a lower yield strength compared to ADC12 but provides good toughness, formability, and excellent extrudability, making it well-suited for applications that require shaping and forming processes.
3. Fluidity and Castability:
ADC12: ADC12 alloy offers good fluidity as well, making it suitable for intricate shapes and thin-walled applications.
A380: A380 alloy generally exhibits better fluidity during the casting process, allowing for more intricate and complex castings.
6063 aluminum alloy also displays good fluidity and castability, it can effectively fill molds with thin walls and complex shapes, but the fluidity might be comparatively lower than ADC12. 6063 is widely used in extrusion processes, where the alloy is pushed through a die to create profiles with uniform cross-sections.
4. Surface Finish:
ADC12: ADC12 can have a slightly rougher surface finish compared to A380, but it can still achieve acceptable finishes for many applications.
A380: A380 typically provides a smoother and more visually appealing surface finish, making it desirable for applications where aesthetics are important.
6063: 6063 aluminum alloy often has a smooth and shiny surface finish, making it suitable for applications that demand an aesthetically pleasing appearance.
5. Applications:
ADC12: ADC12 is widely employed in automotive parts, such as engine components, transmission cases, and chassis components, as well as in electrical and electronic equipment.
A380: A380 is commonly used in automotive components, household appliances, electrical housings, and various structural parts.
6063: 6063 is widely used in architectural extrusions, window frames, door frames, furniture, and other applications that require excellent formability and an attractive finish.