ADC aluminum is a type of material that is standardized by the Japanese Industrial Standards for die casting. Here we’ll explain the term ADC and introduce its material properties and types.
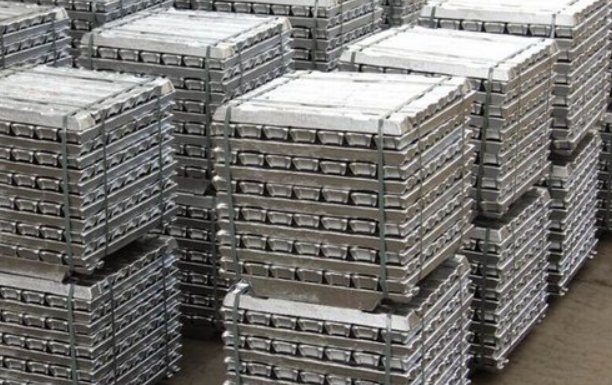
What Is the Full Form of ADC in Material? - ADC Aluminum Explained
ADC stands for Aluminum Die Casting. The term ADC is commonly used to refer to aluminum alloys that are specifically designed and optimized for the die casting process. ADC alloys are widely utilized in various industries for the production of complex and precision components through the die casting method. For example, the term “ADC12” is an alloy designation that provides information about the composition of the aluminum alloy. The “A” signifies aluminum as the primary base metal, the “D” stands for “die casting,” indicating that the alloy is specifically formulated and optimized for die cast production processes, the “C” represents “casting” and signifies that the alloy is intended for casting applications. The number “12” indicates the specific alloy composition. In the case of ADC12, it signifies that the alloy contains approximately 12% silicon as its main alloying element. ADC12 also typically includes small amounts of other elements such as copper, magnesium, and iron.
ADC Material properties
ADC (Aluminum Die Casting) refers to a group of aluminum alloys specifically formulated for the die casting process, here are some general properties commonly associated with ADC alloys:
– High Strength: ADC alloys offer good mechanical strength, providing the ability to withstand loads and stresses. The specific strength can vary based on the alloy composition and heat treatment.
– Lightweight: ADC alloys are lightweight due to the low density of aluminum. This property is advantageous in industries where weight reduction is desired, such as automotive and aerospace.
– Good Corrosion Resistance: ADC alloys typically exhibit good resistance to corrosion, although the level of corrosion resistance can vary depending on the specific alloy and environmental conditions.
– Excellent Castability: ADC alloys have excellent fluidity and castability, allowing for the production of intricate and complex shapes with high precision. They can fill molds with thin walls, fine details, and complex geometries.
– Thermal Conductivity: ADC alloys have good thermal conductivity, enabling efficient heat dissipation. This property makes them suitable for applications where effective heat transfer is required.
– Machinability: ADC alloys are generally machinable and can be easily cut, drilled, and tapped to achieve precise dimensions and features.
– Electrical Conductivity: Aluminum, the base metal of ADC alloys, is known for its good electrical conductivity. Consequently, ADC alloys exhibit favorable electrical conductivity properties.
Types of ADC Aluminum Alloy
– ADC12: ADC12 is one of the most widely used ADC alloys. It typically contains around 9.6-12% silicon, along with small amounts of copper, magnesium, and other elements. ADC12 offers excellent castability, good mechanical properties, and is commonly used in automotive components, electrical housings, and various industrial applications.
– ADC10: ADC10 is another popular ADC alloy with a silicon content ranging from 7.5% to 9.5%. It exhibits good fluidity and castability and is often used for components that require both high strength and excellent surface finish, such as motor housings and pump parts.
– ADC6: ADC6 is an ADC alloy with a silicon content ranging from 3.5% to 5.5%. It offers good fluidity and castability and is commonly utilized in applications that require good corrosion resistance, such as marine components, electrical connectors, and electronic enclosures.
– ADC3: ADC3 is an ADC alloy with a silicon content ranging from 1.8% to 3.0%. It has relatively lower silicon content and offers higher ductility and better machinability compared to other ADC alloys. ADC3 is often used for components that require complex shapes, including automotive parts and general-purpose die-castings.
Difference Between ADC10 and ADC12:
– Silicon Content: ADC10 typically has a silicon content ranging from 7.5% to 9.5%, while ADC12 has a higher silicon content, usually around 9.6% to 12%. The higher silicon content of ADC12 provides improved fluidity during the casting process.
– Strength: ADC12 generally has higher strength compared to ADC10. The higher silicon content in ADC12 contributes to its increased strength, making it suitable for applications that require higher mechanical properties.
– Castability: Both ADC10 and ADC12 offer good castability, but ADC12 generally exhibits better fluidity due to its higher silicon content. This enhanced fluidity allows for the filling of complex molds and the production of intricate shapes with finer details.
– Surface Finish: ADC12 tends to provide a better surface finish compared to ADC10. The higher silicon content in ADC12 helps in achieving smoother and more refined surface finishes, making it preferred for applications where appearance matters.
– Applications: ADC10 is commonly used in applications that require a balance between strength and surface finish, such as motor housings, pump components, and general-purpose die castings. ADC12, with its higher strength and improved surface finish, is often utilized in automotive components, electrical housings, and more demanding applications.