In the realm of aerospace and industrial materials, aluminum alloys continue to play a pivotal role, pushing the boundaries of strength, durability, and performance. Among the standout alloys making waves in 2024 are the refined 7175 and 7475 aluminum alloys, both derived from the formidable 7075 alloy but boasting enhancements that cater to specific applications. Today, we’re going to find out what is 7175, 7475, and 7075, and the differences between them.
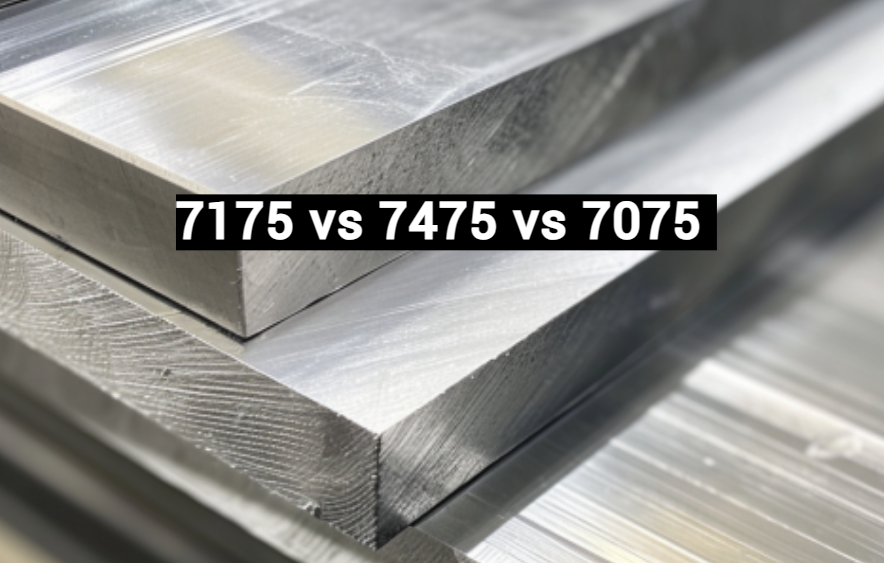
What is 7175 Aluminum?
Composition: Like 7075, 7175 contains zinc as its primary alloying element at around 5-6%. It also contains magnesium, copper, and chromium.
Strength: 7175 has a slightly higher strength than 7075. Its minimum yield strength is 550 MPa compared to 500 MPa for 7075.
Stress corrosion cracking resistance: 7175 has better resistance to stress corrosion cracking than 7075, particularly in marine environments. This makes it more durable.
Machinability: Machinability is similar to 7075 – it work hardens rapidly and requires aggressive machining parameters and frequent tool changes.
Heat treatment: 7175 is also strengthened via the T6 temper (solution heat treat, quench, artificial age). This provides maximum strength benefits.
Applications: Due to its very high strength and good corrosion resistance, 7175 is used in aircraft structures, military vehicles, implants, and other applications requiring robust performance.
Cost: As a specialized high-strength alloy, 7175 typically costs somewhat more than 7075, though both alloys are more expensive than common alloys like 6061.
What is 7475 Aluminum?
7475 aluminum is a very high strength aluminum alloy that is similar to 7075, but with even higher strength properties. Here are some key things to know about 7475 aluminum:
Composition: Like 7075 and 7175 alloys, 7475 contains zinc as its primary alloying element at around 5-6%. It also contains magnesium, copper, and chromium.
Strength: 7475 has the highest strength of this family of alloys. Its minimum yield strength is 621 MPa, significantly higher than 7075 at 500 MPa.
Machinability: Machinability is equally challenging as 7075/7175 due to work hardening. Requires aggressive machining and frequent tool changes.
Welding: Welding characteristics are also very difficult, requiring specialized filler alloys and heat treatments to prevent cracking.
Heat Treatment: Strengthened via the same T6 temper as other alloys – solution heat treat, quench, artificial aging.
Applications: Used in only the most demanding structural applications where extremely high strength to weight is essential, such as aircraft landing gear components.
Cost: As a highly specialized alloy, 7475 typically has a significant premium over 7075/7175 due to development costs and limited production volumes.
What is 7075 Aluminum?
Composition: 7075 contains zinc as its primary alloying element, between 5.1-6.1%. It also contains magnesium, copper, and small amounts of other elements.
Properties: 7075 has excellent mechanical properties, especially strength and fatigue resistance. Its minimum yield strength is 483 MPa (70 ksi).
Density: At 2.81 g/cm3, 7075 has a higher strength-to-weight ratio than many other alloys. This makes it desirable for applications where weight is critical.
Machinability: Due to work hardening, 7075 is difficult to machine. It requires frequent tool changes and slow speeds to avoid excessive tool wear.
Heat Treatment: Solution heat treated and artificially aged (T6 temper), 7075 achieves maximum strength and corrosion resistance.
Applications: Commonly used in aircraft structures, armored vehicles, marine components, etc. where high-strength lightweight parts are needed.
Corrosion Resistance: Better than plain aluminum but prone to stress corrosion cracking. Requires protective coatings or anodizing in many environments.
Weldability: Difficult to weld due to cracking tendencies. Requires special filler alloys and heat treatments when welding.
7175 vs 7475 vs 7075: Which is Better
7175 aluminum alloy improves purity on the basis of 7075 aluminum alloy and is mainly used as die forgings, There are“ 66. T74. Knife 452 has three heat treatment states. Among them, T66 state die forgings have higher static strength than 7075-T6 forgings, and their fatigue, fracture, and stress corrosion resistance are comparable. The static strength of T74 state die forgings and free forgings is comparable to 7075 Jun forgings, and their stress corrosion resistance is between 7075-T73 and T76, while their toughness and fatigue performance are comparable and even better than 7075-T6 forgings. The stress corrosion resistance of T74 state die forgings is significantly higher than that of 7075-T6 state, approaching 7075 Jun forgings -T73 status.
7475 aluminum alloy is a high-purity modification of 7075 alloy, and the thin plate is used in T61 or T761 state with or without aluminum coating. Thick plates have three states: T651-T7651-T7351. The static strength is equivalent to the corresponding state of 7075, but it has better fracture toughness and fatigue crack propagation resistance. The typical value of fracture toughness for thick plates is 40% higher than that of 7075 alloy in the same heat treatment state. Its corrosion resistance and fatigue behavior are comparable to current high-strength aviation aluminum alloys such as 7075.7050 and 2024, and even better in some cases.