Lost-foam casting or LFC is a casting process that is similar to investment casting but not the same, here we are going to introduce six new types of lost foam casting techniques or processes.
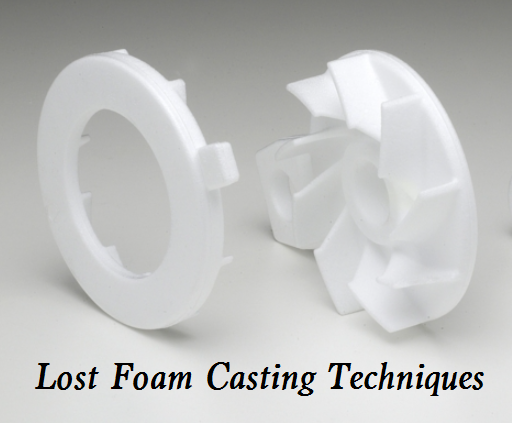
6 New Different Types of Lost Foam Casting Techniques
The lost foam casting technology is a casting method that uses foam plastics to make a full mold with the same structure and size as the parts, which is dipped with fire-resistant adhesive coating, dried, dry sand molding, vibrated and compacted, and then poured with a liquid metal to make the pattern evaporate by heating, so as to obtain a metal part with the same shape as the pattern.
1. Pressure Lost Foam Casting
The pressure lost foam casting technology is a new casting technology that combines the lost foam casting technology with the pressure solidification crystallization technology. It is a casting method in the pressure tank with a sandbox, after the molten metal is poured to vaporize the foam plastic, the pressure tank is quickly sealed, and a certain pressure of a gas is introduced to make the metal liquid solidify and crystallize under pressure. The characteristics of this casting technology are that it can significantly reduce the casting defects such as shrinkage cavity, porosity, and air hole, improve the density of castings, and improve the mechanical properties of castings.
2. Vacuum Low-Pressure EPC
Vacuum low-pressure EPC technology is a new casting technology developed by combining the negative-pressure EPC method with the low-pressure anti-gravity casting method. The characteristics of vacuum low-pressure EPC technology are as follows: it combines the technical advantages of low-pressure casting and vacuum EPC, completes the mold-filling process under controlled air pressure, and greatly improves the casting mold-filling ability of the alloy. Compared with die casting, the equipment investment is small, the casting cost is low, and the casting can be strengthened by heat treatment; Compared with sand casting, the casting process has high precision, small surface roughness, high productivity, and good performance; Under the action of counter gravity, the straight gate becomes the feeding and shortening channel, the loss of pouring temperature is small, the liquid alloy is fed and solidified under controllable pressure, and the gating system of alloy castings is simple and effective, the yield is high, and the structure is dense; The low pouring temperature of vacuum low-pressure EPC is suitable for various nonferrous alloys.
3. Vibration EPC
Vibration EPC casting technology is to apply a certain frequency and amplitude of vibration in the EPC process so that the casting can solidify under the action of the vibration field. Because a certain time of vibration is applied to the metal solution in the EPC solidification process, the vibration force causes the relative movement between the liquid phase and the solid phase, which makes the dendrite break, increases the crystal core in the liquid phase, and makes the final solidification structure of the casting refined, and the mechanical properties improved. This technology makes use of the existing compact vibration table in EPC, through the mechanical vibration generated by the vibration motor, so that the metal liquid can nucleate under the dynamic excitation, and achieve the goal of refining the structure. It is a simple, low-cost, environment-friendly method.
4. Semi-solid Lost Foam Casting
Semi-solid lost foam casting technology is a new casting technology that combines lost foam casting technology with semi-solid technology. Because the process is characterized by controlling the relative proportion of liquid and solid, it is also called transformation control semi-solid forming. This technology can improve the density of castings, reduce segregation, and improve dimensional accuracy and casting performance.
5. EPC Shell Mold Casting
EPC shell mold casting technology is a new casting method that combines investment casting technology with EPC. This method is a new precision casting method, in which several layers of refractory materials are coated on the surface of the foam plastic pattern with the same shape as the part made by the foam mold, and after it is hardened and dried, the foam plastic pattern is burned, vaporized and disappeared to form a mold shell, which is then baked and poured to obtain castings with high dimensional accuracy. It has the characteristics of large pattern size and high precision in lost foam casting, as well as the advantages of shell precision and strength in investment casting. Compared with ordinary investment casting, it is characterized by the low cost of foam plastic pattern material, convenient bonding and combination of patterns, easy vaporization, and disappearance, overcoming the problem of investment deformation caused by easy softening of investment casting pattern material, and being able to produce various alloy complex castings of large size.
6. EPC Suspension Casting Technology
EPC suspension casting technology is a new practical casting technology that combines the EPC process with suspension casting. The technological process is that after the molten metal is poured into the mold, the foam plastic pattern is gasified, and the suspending agent is mixed in the riser model (or placed in a specific position of the pattern, or made into a foam pattern with the suspending agent and EPS) reacts with the molten metal to improve the overall (or partial) organizational performance of the casting.