When it comes to high-performance steels, 440 Steel and D2 stand out as two of the most popular choices among knife makers, toolmakers, and manufacturers. While both materials offer exceptional performance characteristics, they serve distinctly different purposes and excel in unique ways. The 440 series, known for its corrosion resistance and versatility, brings a different set of strengths to the table compared to D2, which is celebrated for its incredible wear resistance and edge retention. Understanding these differences is crucial for anyone looking to make an informed decision about which steel best suits their specific needs, whether for cutlery, industrial tools, or precision instruments. In this 440 stainless steel guide, we’ll talk about the differences between 3 types of 440 and D2.
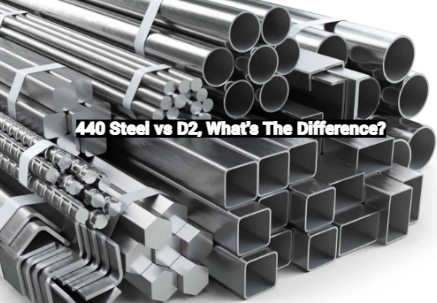
What’s 440 Steel?
Steel 440 is a high-carbon martensitic stainless steel that comes in three variants (440A, 440B, and 440C), characterized by its significant carbon content (0.95-1.20%) and chromium content (16-18%). This composition gives the steel exceptional hardness, strength, and wear resistance, making it a preferred choice for applications requiring durability such as knife blades, surgical instruments, and bearings. The martensitic structure, combined with these high carbon and chromium levels, creates a material that effectively balances toughness with corrosion resistance.
The Advantages Of 440 Stainless Steel
440 stainless steel is a family of high-carbon, martensitic stainless steels, and the term “440 stainless steel” generally refers to three grades: 440A, 440B, and 440C, each with distinct advantages. However, regardless of the specific grade within the 440 series, this family of steels shares several key benefits:
- Excellent Corrosion Resistance
440 stainless steel provides a high level of resistance to corrosion, especially when compared to carbon steels. This makes it ideal for use in environments that involve exposure to moisture, chemicals, or saltwater. While 440A offers the best corrosion resistance of the three grades, even 440C holds up well in many outdoor and marine applications. - Good Edge Retention
440 stainless steel is known for its ability to maintain a sharp edge, especially in higher grades like 440B and 440C. This is due to its higher carbon content, which allows for greater hardness after heat treatment. Knives and cutting tools made from 440C, for example, are able to hold an edge for longer periods, making them ideal for heavy-duty or precision cutting applications. - High Hardness and Wear Resistance (Especially in 440C)
The high carbon content in 440 stainless steels, particularly 440C, enables these steels to achieve a high Rockwell hardness (58-62 HRC). This makes them highly resistant to wear, abrasion, and deformation, which is crucial for tools, knives, and bearings that undergo constant stress and friction. - Toughness and Durability
Although 440C is harder and less tough than 440A or 440B, the lower-carbon variants (440A and 440B) still offer good toughness and impact resistance. This makes them more durable and less likely to chip or break under stress, especially in applications that require more impact resistance. - Ease of Heat Treatment
440 stainless steel responds well to heat treatment, allowing for customization of its hardness and mechanical properties. This versatility in heat treatment gives manufacturers more control over the final product’s performance, enabling 440 stainless steel to be used in a wide range of applications, from knives to industrial tools and bearings.
The Applications Of 440 Stainless Steel
Cutlery and Knives
In the culinary world, 440 stainless steel has established itself as a premier material for knife-making and cutlery. Its high carbon content enables excellent edge retention, making it ideal for professional chef knives, hunting knives, and everyday kitchen cutlery. The material’s ability to maintain sharpness, combined with its corrosion resistance, ensures longevity and reliable performance in both professional kitchens and household use. The grade’s hardness makes it particularly effective for precision cutting tasks while remaining relatively easy to maintain and sharpen.
Surgical Instruments
The medical field heavily relies on 440 stainless steel, particularly 440C, for surgical instruments due to its exceptional properties. Surgical scalpels, dental tools, and medical scissors benefit from the material’s ability to maintain an extremely sharp edge while meeting stringent medical sterilization requirements. The high chromium content provides necessary corrosion resistance against repeated sterilization processes, while its hardness ensures precise cutting edges crucial for delicate surgical procedures. The material’s durability also ensures cost-effectiveness through extended instrument life.
Bearings and Bushings
In mechanical applications, 440 stainless steel excels in bearing and bushing components due to its outstanding wear resistance and strength. The material’s high hardness makes it perfect for ball bearings and roller bearings that must withstand continuous mechanical stress and friction. Its dimensional stability under varying temperatures and loads ensures reliable performance in critical mechanical systems. The combination of hardness and corrosion resistance makes it particularly valuable in environments where traditional bearing materials might fail.
Industrial Valves
The valve industry extensively uses 440 stainless steel for its excellent combination of strength and corrosion resistance. Control valves, gate valves, and check valves made from this material demonstrate superior performance in controlling fluid flow under demanding conditions. The material’s resistance to various corrosive media, coupled with its mechanical strength, makes it ideal for applications in chemical processing, oil and gas, and other industrial environments where valve reliability is crucial.
Marine Hardware
In marine applications, 440 stainless steel proves invaluable for hardware components exposed to harsh saltwater environments. Boat fittings, fasteners, and underwater equipment benefit from the material’s high corrosion resistance and strength. While not as corrosion-resistant as some other stainless steel grades, proper maintenance and coating can make 440 stainless steel highly effective in marine applications where both strength and corrosion resistance are required.
What Are The Differences Between 440A, 440B & 440C?
The differences between 440A, 440B, and 440C stainless steels primarily lie in their carbon content and the resulting hardness, corrosion resistance, and toughness of each grade. They all belong to the 440 family of stainless steels, which are high-carbon, martensitic steels used for making blades, knives, and other tools. Here’s a breakdown of their key characteristics:
1. 440A
440A stainless steel has a carbon content of 0.60% to 0.75%, making it softer than 440B and 440C, with a hardness range of 55-58 HRC. It offers good corrosion resistance and excellent toughness, making it suitable for applications that require a balance of durability and flexibility, such as kitchen knives, medical instruments, and general-purpose cutting tools. However, due to its lower carbon content, it does not hold an edge as well as the higher-carbon 440B or 440C steels.
2. 440B
440B stainless steel, with a carbon content of 0.75% to 0.90%, strikes a middle ground between the softer 440A and the harder 440C. It reaches a hardness of 58-60 HRC and provides a good balance of hardness, corrosion resistance, and toughness, making it suitable for knife blades, industrial tools, and components that need a sharper edge and more wear resistance than 440A, but still retain some toughness for impact resistance.
3. 440C
440C stainless steel, with a carbon content of 0.95% to 1.20%, is the hardest and most wear-resistant of the three, achieving a hardness of 58-62 HRC. Its high carbon content allows for excellent edge retention and resistance to wear, making it ideal for high-performance knives, ball bearings, and cutting tools. However, the increased hardness comes at the expense of toughness, as 440C is more brittle than 440A or 440B, making it less suitable for applications involving heavy impacts or bending forces.
440A vs 440B vs 440C, Which to choose?
- If you need a good balance of corrosion resistance and edge retention without excessive brittleness, 440A is a solid choice.
- For applications where you need a bit more hardness but still a reasonable level of toughness, 440B is ideal.
- If maximum hardness and wear resistance are needed (with less concern for toughness), 440C is the best option.
440 Steel vs D2, What’s The Difference?
The difference between 440 steel (which includes 440A, 440B, and 440C) and D2 tool steel lies primarily in their composition, properties, and intended applications. Both are high-performance steels, but they excel in different areas, making them suited to different tasks. Here’s a breakdown of the key differences between 440 steel and D2 steel:
Property | 440 Steel | D2 Steel |
---|---|---|
Steel Type | Martensitic Stainless Steel | High-Carbon, High-Chromium Tool Steel (Semi-Stainless) |
Carbon Content | 0.60% to 1.20% (depending on grade) | 1.40% to 1.60% |
Chromium Content | 12% to 15% | 11% to 13% |
Other Alloying Elements | Primarily chromium (for corrosion resistance) | Molybdenum, Vanadium (for wear resistance) |
Hardness (HRC) | 440A: 55-58 HRC, 440B: 58-60 HRC, 440C: 58-62 HRC | 59-62 HRC |
Wear Resistance | Good (best in 440C, but less than D2) | Excellent (better than 440 steel) |
Corrosion Resistance | Excellent (especially in 440A and 440B) | Good (less corrosion-resistant than 440 steel) |
Toughness | Fair to good (best in 440A) | Fair (tougher than 440C but not as tough as 440A) |
Edge Retention | Good (best in 440C) | Excellent (holds edge longer than 440 steel) |
Sharpening | Easier to sharpen (especially 440A) | Harder to sharpen (due to higher hardness) |
Primary Use | Knives, bearings, surgical instruments, cutlery | Heavy-duty cutting tools, dies, industrial knives |
Cost | Generally more affordable than D2 | Typically more expensive than 440 steel |
Suitability for Tough Jobs | Moderate (440A and 440B more suitable for tougher tasks than 440C) | Excellent (D2 is tougher and better suited for heavy cutting tasks) |