Zinc alloy die casting is a kind of pressure casting part. It uses a pressure casting machine die casting machine equipped with a casting mold to pour the heated liquid zinc or zinc alloy into the feed inlet of the die casting machine. After being cast by the die casting machine, zinc parts or zinc alloy parts with limited shape and size of the mold are cast. Such parts are usually called zinc alloy die castings. The main characteristics of zinc alloy die casting are that the melting point of zinc alloy is low, and the melting process occurs when the temperature reaches 400 ℃, which is easier to form in zinc alloy die casting. We are going to talk about 10 things you should know when designing zinc alloy die castings.
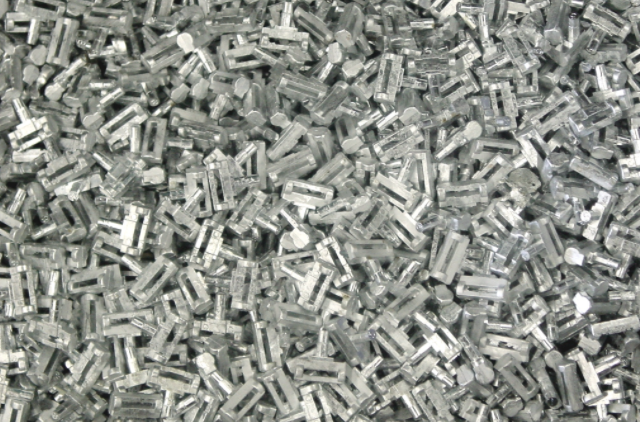
The design of zinc alloy die castings roughly includes 10 aspects:
-Thickness design
-Stiffener design
-Fillet design
-Slope design
-Logo design
-Shrinkage design
-Hole groove design
-Thread design
-Dimensional accuracy design
-Geometric tolerance design
Thickness design of zinc alloy die castings
Stiffener design
Generally speaking, the thickness of the stiffener is 2/3 to 3/4 of the wall thickness, and the slope shall be set to facilitate demolding.
Fillet design
The maximum basis for fillet design is the wall thickness, which is usually multiplied by a coefficient. For the fillet of zinc alloy die castings with equal wall thickness transition, this coefficient can be taken as 0.25~1, that is, the minimum is one-quarter of the material thickness and the maximum is one material thickness.
Slope design
For the draft angle of zinc alloy die castings, the minimum release angle of the mating surface is 10 points and 15 points, corresponding to the outer surface and inner surface respectively. For nonmating surfaces, the minimum draft angle is 15 points and 45 points, corresponding to the outer surface and the inner surface respectively.
Text pattern and logo
This is relatively simple. Generally, the convex pattern is adopted, and the height is greater than 0.3 mm. Of course, laser printing or color film embossing can also be used.
Shrinkage design
Generally speaking, the free linear shrinkage of zinc alloy is 0.6~0.8%, and the hindered shrinkage is 0.3~0.6%. If possible, the casting CAE analysis software can be used to conduct a solidification stress simulation to determine the actual shrinkage of the casting.
Hole groove size design
Generally, the hole and groove size of zinc alloy has a minimum value, which cannot be too small, otherwise, the core pulling will easily lead to fracture. Moreover, the size of the hole groove is limited by the depth, because the hole groove must be set with a certain slope to pull the core. Generally, the minimum diameter is 1 mm, and it can reach 0.7 mm at the minimum. For the depth, the blind hole can be taken as 4 times the minimum diameter and the through-hole as 8 times. The inclination in the hole is 0-15 points.
Thread design
Generally speaking, the minimum pitch that can be directly cast by zinc alloy die casting is 0.75 mm, the minimum thread outer diameter is 6 mm, and the maximum thread length is 8 times the pitch.
Dimensional tolerance design
The dimensional tolerance grade is ct4~ct6, and castings are of different sizes.
Geometric tolerance design
The form and position tolerances of zinc alloy die castings are shown in the figure above, including flatness, parallelism, and cordiality tolerances.