The die casting process is complex, and there are many factors affecting the quality of die casting products. Due to the loose control of raw materials, unreasonable process plan, improper production operation and other reasons, die casting defects have always been a major problem perplexing die casting service enterprises. If the defects in die casting are not solved properly, the quality of castings will be affected. In this article, we are going to be covering the common defects found in castings, why they happen, how to detect them and how to prevent them.
What Are Die Casting Defects?
A casting defect is an irregularity in a metal casting process that is very undesirable and some major defects can cause castings to be rejected. It can also cause a part to become a danger to the end-user and potentially a guest strophic failure. It is vital to understand the different defects in die castings and how to identify them.
Typical defects that occur inside or on the surface of casting, such as shrinkage, hot tears and their causes and countermeasures are listed below.
– Gas porosity defects
– Short shots
– Cold shut defects
– Hot tears
– Excessive flash
– Shrinkage
Types Of Die Casting Defects And How To Prevent Them
Gas Porosity
This is the formation of bubbles within the casting after it has cooled. This occurs because most liquid metals can hold a large amount of dissolved gas, but the solid form of the same material cannot, so the gas forms of bubbles or voids within the material as it cools. We can see a typical porosity defect. The best way to check castings for porosity is with X-ray equipment for non-destructive inspection or simply by cutting the casting into sections and checking for voids, this is a destructive test so cannot be carried out on all samples. This defect depending upon the severity of the porosity can lead to major defects and high scrap rates. Critical component example would be a tunnel extraction fan blades.
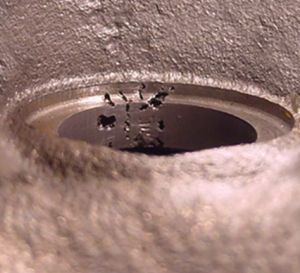
Solution:
Use good melting practices by melting the material in a vacuum, around low-solubility gases, or under a flux, which prevents air from touching the molten metal. If nothing else works, try pouring the molten metal at a lower temperature during the casting to keep it from absorbing as much gas.
Shrinkage
Shrinkage defects appear because metal alloys shrink as they cool. It is normal for an alloy piece to shrink as it solidifies (which should be included in calculations when designing the mold). However, defects occur when the metal shrinks unevenly, causing it to either distort the shape of the final product or create interior holes. This can also stress the metal. Shrinkage defects contain open shrinkage defects, closed shrinkage defects and warping.
Solution:
Adjust the mold temperature or redesign the mold.
Cold Shut
Cold shut defect cool shuts occur when two fronts of liquid metal do not fuse properly in the die cavity, leaving a weak spot. We could see an example in this picture below where the two liquid metal fronts have met but not fused leaving this obvious failure mode. Best way to check castings for cold shut is to check them by eye as this defect will be visible. The cold shot will either be in just a section or right across the entire casting. This defect will result in the castings being scrapped as the casting has a weak point will not have full integrity.
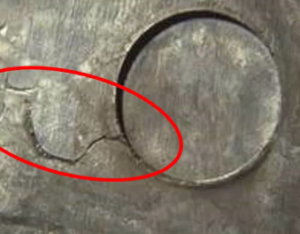
Solution:
Raise the mold temperature, the molten metal temperature, and the plunger speed or change the position and size of the gate.
Cracks
Cracks are material breakage caused by stress inside and outside the material. The first ones are created during solidification and cooling phase: due to cavity geometry material is not allowed to shrink in its natural directions, what results is residual stress that can generate cracks inside the mould or deformations after ejection. The second ones are caused by external forces on components: these forces can be found during parts ejection from the mould or cutting phase.
Solution:
Redesign the shape or change the extrusion position.
Hot Tear
Hot tears are the formation of irreversible failure or a crack in the still semi solid casting. This occurs in the solidification phase of the casting process. In the below image we can see a hot tear defect, the cracks are clearly obvious. Best way to check castings for hot tears is to check them by eye as most of these defects will be visible. However in some cases it may be necessary to respect through magnification or even X-ray. This defect will result in the castings being scrapped as the casting has a weak point and will not have full integrity.
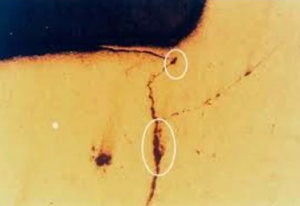
Solution:
With hot tears, the mold is the key. The chances can be greatly reduced by using well-designed molds that evenly cool the casting and that deform the proper way in hot conditions.
Excessive Flash
Excessive flash is the additional unrequired material attached to the main casting. This is often caused by either the injection pressure is too high or the clamp pressure is too low resulting in the injected metal flowing out between the die halves. The image below clearly shows this casting has way too much flash. This defect is visible with the eye. This will not result in scrapped components but will incur additional cost for post casting finishing to remove the excess flash.
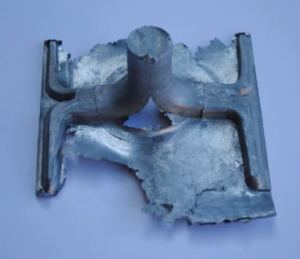
Solution:
Remedy this issue by reassembling the mold and cores.
Short Shot Defect
A short shot or miss run occurs when the leak methyl does not completely fill the mold cavity leaving an unfilled portion. We can clearly see this unfilled portion in this casting in this image. This is a short shot defect, best way to check castings for short shots is to expect the final castings to assure all dimensions have been met. Most short-shot defects are obvious, but some may be subtle and not obvious to the eye. This defect will result in castings being scrapped as the final casting shape has not been produced. Potential corrective actions for this is to increase shop volume, increase injection pressure, increase dye temperature.
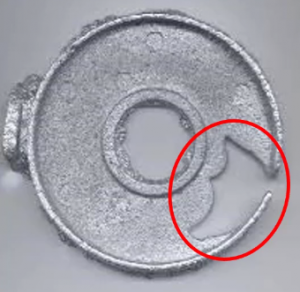